Welcome to My Blog!
Before we dive into the content, I’d love for you to join me on my social media platforms where I share more insights, engage with the community, and post updates. Here’s how you can connect with me:
Facebook:https://www.facebook.com/profile.php?id=61559060896490
Now, let’s get started on our journey together. I hope you find the content here insightful, engaging, and valuable.
Table of Contents
Introduction
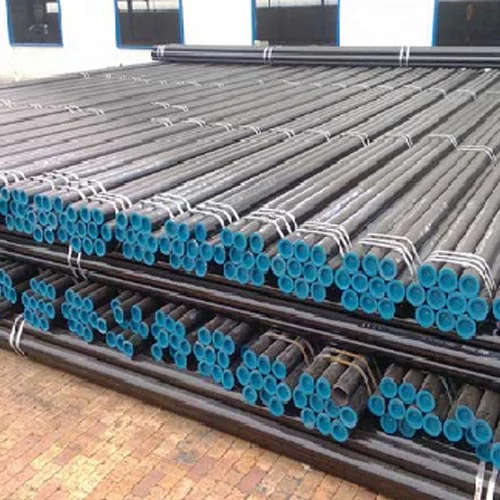
You might not often consider the types of boiler tubes in your industrial system, but they are crucial for the performance, longevity, and safety of boilers in power generation, chemical processing, and manufacturing. The right choice significantly impacts energy efficiency, operational costs, and environmental footprint.
Understanding the various types of boiler tubes is vital for engineers, procurement specialists, and facility managers to make informed decisions that save time, reduce failures, and enhance safety. This guide will cover their classifications, materials, applications, and maintenance to help you boost your system’s efficiency.
Understanding the Basics: What Are Boiler Tubes?
Before diving into the types of boiler tubes, it’s important to grasp what these components actually do. Boiler tubes are integral parts of boilers, where water is heated and converted into steam for various applications like power generation, heating, and industrial processes.
Boiler tubes must withstand extreme temperatures, pressures, and corrosion environments, especially when operating in energy-intensive sectors. This is why high-quality seamless steel tubes are the preferred choice—offering superior strength, longer service life, and reduced risk of leakage or failure compared to welded alternatives.
Boiler tubes generally fall into two main categories:
1. Water Tube Boiler Tubes
Water flows inside the tubes while hot gases circulate around them. These are commonly used in high-pressure applications like power plants and industrial facilities.
2. Fire Tube Boiler Tubes
Hot gases flow through the tubes while water surrounds them. They are used for low- to medium-pressure systems and are popular in commercial heating applications.
Types of Boiler Tubes: Classifications That Affect Performance
Knowing the correct types of boiler tubes ensures that you match material properties to specific system needs. There is no one-size-fits-all solution, as each tube type has unique strengths, weaknesses, and ideal applications.
1. Seamless Boiler Tubes
Seamless steel tubes are manufactured without welding, making them perfect for high-pressure applications. Their uniform structure reduces the risk of weak points or failures under pressure.
Applications: Power generation, petrochemical plants, and refineries where durability is critical.
Advantages:
- High strength
- Excellent corrosion resistance
- Smooth internal surface for better flow efficiency
2. Welded Boiler Tubes
These tubes are manufactured by welding the edges of steel plates or strips. Suitable for lower-pressure environments but less reliable in high-stress applications compared to seamless tubes.
Applications: HVAC systems, low-pressure industrial boilers.
Advantages:
- Cost-effective for low-pressure usage
- Easily customizable for specific shapes and sizes
3. Alloy Steel Boiler Tubes
Made with alloying elements such as chromium, molybdenum, or nickel, these tubes offer superior heat resistance and strength.
Applications: High-temperature environments such as thermal power plants or chemical processing facilities.
Advantages:
- Outstanding thermal stability
- Enhanced oxidation resistance
4. Carbon Steel Boiler Tubes
These are widely used because of their affordability and decent mechanical properties, making them suitable for medium-pressure boiler systems.
Applications: Food processing, textile, and general industrial boilers.
Advantages:
- Economical
- Good mechanical strength
5. Stainless Steel Boiler Tubes
Stainless steel tubes resist corrosion and scaling, especially important in harsh environments involving water and steam.
Applications: Pharmaceutical production, food industries, and marine boilers.
Advantages:
- Excellent corrosion resistance
- Longevity under aggressive conditions
Key Factors in Selecting the Right Types of Boiler Tubes
Choosing from various types of boiler tubes is not simply a matter of cost—it’s about matching performance characteristics with operating conditions. Below are critical factors to consider:
Material Composition
The chemical makeup of the tube determines its thermal resistance, corrosion behavior, and overall strength. Alloy and stainless steels generally outperform carbon steel in harsh environments.
Pressure and Temperature Ratings
Different types of boiler tubes handle varying levels of pressure and temperature. Seamless alloy tubes are best for extreme conditions, whereas carbon steel is suitable for moderate applications.
Corrosion Resistance
Corrosion can severely limit the life expectancy of boiler tubes. Industries dealing with high moisture, chemicals, or salt exposure should opt for stainless or alloy steels.
Wall Thickness and Diameter
Proper sizing is crucial for maintaining fluid dynamics and avoiding excessive thermal stresses or vibration.
Certifications and Standards
Ensure tubes meet international standards like ASTM, ASME, or EN to guarantee performance and safety.
Comparative Table of Common Types of Boiler Tubes
Type of Boiler Tube | Material | Typical Applications | Key Properties | Advantages |
---|---|---|---|---|
Seamless Boiler Tubes | Carbon/Alloy Steel | Power plants, refineries | High strength, smooth internal surface | Excellent for high pressure systems |
Welded Boiler Tubes | Carbon Steel | HVAC, low-pressure boilers | Cost-effective, customizable | Suitable for lower stress systems |
Alloy Steel Boiler Tubes | Alloy Steel (Cr, Mo) | Thermal plants, chemical plants | Heat resistant, durable | Handles extreme temperatures well |
Carbon Steel Boiler Tubes | Carbon Steel | General industrial boilers | Good mechanical properties | Economical choice for medium pressure |
Stainless Steel Tubes | Stainless Steel | Pharma, food processing, marine | Corrosion and scaling resistant | Long-lasting, ideal for aggressive environments |
Installation and Maintenance Tips for Different Types of Boiler Tubes
Proper installation and maintenance can extend the life of any types of boiler tubes you select. Here are essential best practices:
Pre-Installation Inspection
- Verify chemical composition certifications.
- Check for physical defects such as dents or cracks.
- Ensure dimensions meet design specifications.
During Installation
- Maintain correct alignment to reduce thermal stress.
- Use compatible welding materials when necessary.
- Employ experienced welders for seamless and alloy tubes.
Post-Installation Maintenance
- Conduct regular ultrasonic thickness testing.
- Apply protective coatings for corrosion-prone environments.
- Schedule periodic cleaning to prevent scale buildup.
Benefits of Using the Right Types of Boiler Tubes
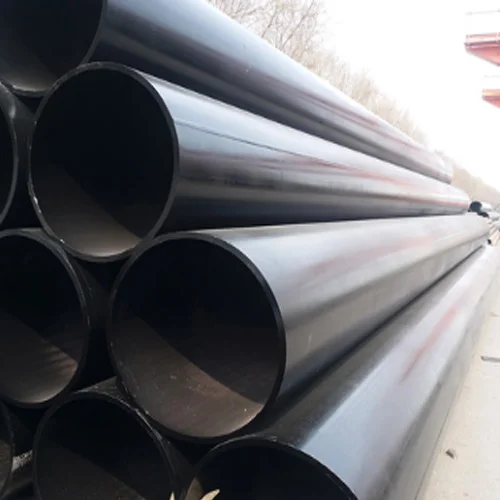
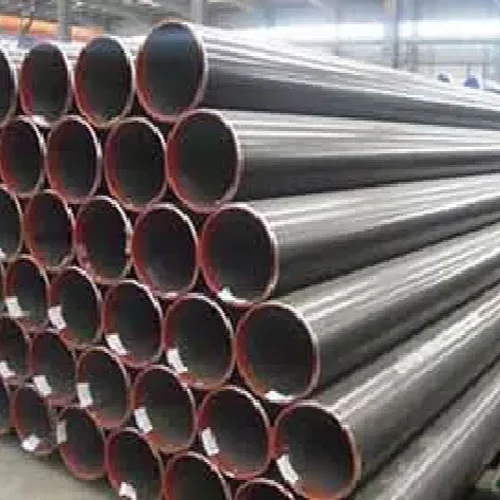
Choosing the suitable types of boiler tubes can significantly impact operational efficiency and safety. Here are the key benefits:
- Improved Heat Transfer Efficiency: Proper tubes enhance the transfer of thermal energy, reducing fuel consumption.
- Extended Service Life: Durable materials resist wear, corrosion, and thermal fatigue, leading to fewer replacements.
- Reduced Downtime: Quality tubes minimize failure risks and unexpected outages, ensuring continuous operations.
- Lower Maintenance Costs: Better performance reduces the need for frequent inspections and repairs.
- Environmental Impact: Efficient tubes decrease emissions by optimizing fuel usage.
Conclusion
The role of boiler tubes in industrial and commercial applications cannot be underestimated. Selecting the appropriate types of boiler tubes—whether seamless, alloy, stainless, or carbon steel—is the key to ensuring safety, reliability, and efficiency in boiler systems.
Don’t rush this decision. Evaluate your process needs, operating conditions, and future scalability before settling on a tube type. Consulting with experienced suppliers and engineers will help you align product specifications with operational demands for maximum long-term benefit.
Remember, the right tube today can save you millions tomorrow—not just in replacement costs but in energy savings, downtime prevention, and peace of mind.
FAQ
What are the main types of boiler tubes used in industrial applications?
The most common types of boiler tubes include seamless, welded, alloy steel, carbon steel, and stainless steel tubes. Each type offers unique properties suited for specific pressure, temperature, and corrosion conditions.
Why are seamless boiler tubes preferred for high-pressure boilers?
Seamless tubes offer superior strength, uniformity, and resistance to pressure-induced failures compared to welded tubes, making them ideal for high-pressure and high-temperature environments.
Can I use carbon steel tubes in corrosive environments?
Carbon steel tubes are affordable but lack corrosion resistance. For corrosive environments, stainless or alloy steel tubes are recommended.
How often should boiler tubes be inspected?
Inspection frequency depends on the operating environment, but a general rule is to perform non-destructive testing (NDT) and visual inspections annually or as required by industrial standards.