Introduction
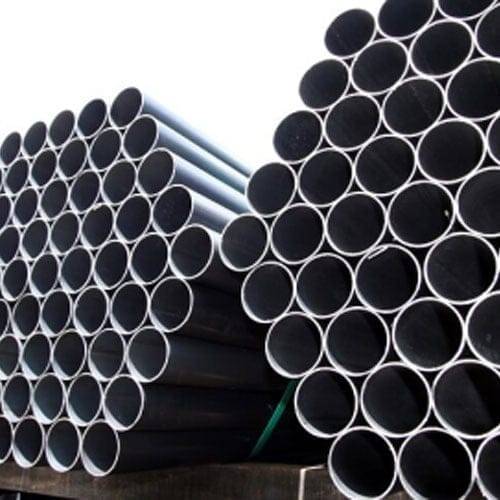
Mechanical tubing is an essential component in various industrial applications, ranging from construction and automotive to aerospace and manufacturing. Understanding mechanical tubing dimensions is crucial for ensuring the correct selection and application of tubing in your projects. This blog will provide a comprehensive overview of mechanical tubing dimensions, including key terms, measurement standards, and considerations for choosing the right tubing for your needs.
Understanding Mechanical Tubing Dimensions
Mechanical tubing dimensions are fundamental to selecting the appropriate tubing for specific applications. These dimensions typically include outside diameter (OD), inside diameter (ID), wall thickness, and length. Let’s break down these key dimensions:
- Outside Diameter (OD):
- Definition: The total diameter of the tubing, including the wall thickness.
- Importance: Affects the tubing’s compatibility with fittings and the space available in the installation area.
- Inside Diameter (ID):
- Definition: The diameter of the hollow portion of the tubing.
- Importance: Determines the flow capacity and pressure rating of the tubing.
- Wall Thickness:
- Definition: The thickness of the tubing’s walls, calculated as the difference between OD and ID, divided by two.
- Importance: Influences the tubing’s strength, pressure rating, and overall durability.
- Length:
- Definition: The total length of the tubing.
- Importance: Affects how the tubing is used in applications, such as fitting into specific spaces or connecting various components.
Standards and Specifications
Mechanical tubing dimensions are standardized to ensure consistency and compatibility across different applications. Key standards and specifications include:
- ASTM Standards:
- ASTM A513: Covers specifications for welded mechanical tubing with different grades and sizes.
- ASTM A500: Specifies cold-formed welded and seamless carbon steel structural tubing.
- ISO Standards:
- ISO 9001: Provides guidelines for quality management systems, ensuring that mechanical tubing meets international quality standards.
- ISO 6507: Defines the hardness testing of metallic materials, relevant for assessing tubing strength.
- ANSI Standards:
- ANSI B36.10M: Defines dimensions for welded and seamless carbon steel pipes, applicable to mechanical tubing.
Table: Common Mechanical Tubing Dimensions
Tubing Size (inches) | Outside Diameter (OD) | Inside Diameter (ID) | Wall Thickness | Length |
---|---|---|---|---|
1/2 x 0.065 | 0.500 | 0.370 | 0.065 | 20 ft |
1 x 0.120 | 1.000 | 0.760 | 0.120 | 20 ft |
2 x 0.250 | 2.000 | 1.500 | 0.250 | 20 ft |
3 x 0.375 | 3.000 | 2.250 | 0.375 | 20 ft |
Factors to Consider When Choosing Mechanical Tubing
Selecting the right mechanical tubing involves considering various factors to ensure it meets your application needs:
- Material Type:
- Carbon Steel: Commonly used for structural applications due to its strength and affordability.
- Stainless Steel: Offers superior corrosion resistance, suitable for harsh environments.
- Aluminum: Lightweight and resistant to corrosion, ideal for applications where weight is a concern.
- Application Requirements:
- Pressure Rating: Ensure the tubing can withstand the operational pressure.
- Temperature Tolerance: Check the tubing’s ability to handle the temperatures in your application.
- Tolerance and Precision:
- Dimensional Tolerance: Verify that the tubing dimensions adhere to industry standards for a proper fit and function.
- Surface Finish: Consider the tubing’s surface quality, which can affect performance and appearance.
Applications of Mechanical Tubing
Mechanical tubing is used in a wide range of applications, each requiring specific dimensions and properties:
- Construction:
- Structural Supports: Tubing is used for beams and columns, providing support and stability.
- Frameworks: Used in scaffolding and structural frameworks for building structures.
- Automotive:
- Exhaust Systems: Tubing is used for exhaust pipes and mufflers, requiring high durability and temperature resistance.
- Chassis and Frames: Provides structural support in vehicle frames and components.
- Aerospace:
- Aircraft Components: Tubing is used for fuel lines, hydraulic systems, and structural elements in aircraft.
- Precision Requirements: Demands high precision and material strength to ensure safety and performance.
Maintenance and Inspection
Proper maintenance and inspection of mechanical tubing are essential for ensuring its longevity and performance:
- Regular Inspections:
- Visual Checks: Look for signs of wear, corrosion, or damage.
- Dimensional Checks: Ensure that the tubing maintains its specified dimensions and tolerances.
- Cleaning and Maintenance:
- Cleaning: Remove contaminants and buildup that could affect performance.
- Repairs: Address any damage or wear promptly to prevent failures.
Case Studies: Successful Applications of Mechanical Tubing
Examining case studies can provide insight into the practical use of mechanical tubing in various industries:
- Case Study 1: High-Rise Building Construction
- Project: Construction of a high-rise office building.
- Challenge: Need for durable, high-strength structural supports.
- Solution: Use of carbon steel mechanical tubing for support beams and columns.
- Outcome: Enhanced structural integrity and safety for the building.
- Case Study 2: Automotive Exhaust System
- Project: Development of a high-performance exhaust system for a sports car.
- Challenge: Requirement for lightweight, corrosion-resistant tubing.
- Solution: Use of stainless steel mechanical tubing with precise dimensions.
- Outcome: Improved performance and durability of the exhaust system.
Future Trends in Mechanical Tubing
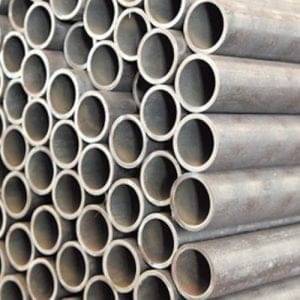
The mechanical tubing industry is evolving with advancements that enhance its performance and applications:
- Advanced Materials:
- High-Strength Alloys: Development of new alloys with improved strength and durability.
- Composite Tubing: Incorporation of composite materials for lightweight and high-strength applications.
- Manufacturing Technologies:
- Precision Machining: Advancements in manufacturing techniques for more precise and customized tubing dimensions.
- Automated Production: Use of automated systems for consistent quality and efficiency.
Conclusion
Understanding mechanical tubing dimensions is crucial for selecting the right tubing for various applications. By familiarizing yourself with key dimensions, standards, and considerations, you can ensure that the tubing you choose meets your project’s requirements. Whether for construction, automotive, or aerospace applications, mechanical tubing plays a vital role in providing strength, durability, and functionality.
FAQ
Q:What is the difference between outside diameter (OD) and inside diameter (ID)?
A:The OD is the total diameter of the tubing, including the wall thickness, while the ID is the diameter of the hollow portion inside the tubing.
Q:How do I determine the appropriate wall thickness for my application?
A:The wall thickness should be selected based on the required strength, pressure rating, and durability needs of your application.
Q:What standards should I consider for mechanical tubing?
A:Key standards include ASTM A513, ASTM A500, ISO 9001, and ANSI B36.10M, which ensure quality and compatibility.
Q:Can mechanical tubing be used for high-temperature applications?
A:Yes, but you must select tubing material that is rated for high temperatures, such as stainless steel or specialized alloys.
Q:How often should mechanical tubing be inspected?
A:Regular inspections should be conducted to check for signs of wear, corrosion, or damage, and to ensure that dimensions remain within specified tolerances.