Seamless Steel Pipe
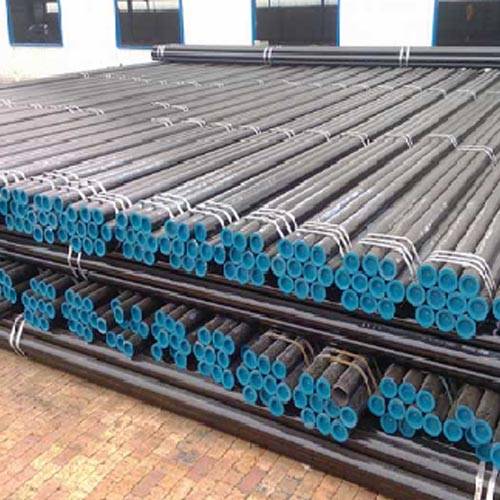
Seamless Steel Pipe
- Pipe Variety: Seamless Pipe, Seamless Carbon Steel Pipe, Carbon steel Seamless Pipe, Hot Rolled Seamless Steel Pipe, Cold Drawn Seamless Steel Pipe, Cold Rolled Seamless Steel Pipe.
- Application: For High Temperature Service, High Temperature Fluids Transmission (oil,gas, water, steam etc.)
- Specification: OD:1/8"~48"(10.3 ~1219mm)WT: SCH 10 ~ 160, SCH STD, SCH XS, SCH XXS LENGTH: Fixed Length (5.8/6/11.8/12mtr), SRL, DRL WT: 0.5mm~8.0mm LENGTH: Fixed Length(5.8/6/11.8/12mtr), SRL, DRL
- Standard: ASTM A106, Grade A/B/C+
- Ends: Square Ends/Plain Ends (straight cut, saw cut, torch cut), Beveled/Threaded Ends
- Surface: Bare, Lightly Oiled, Black/Red/Yellow Painting, Zinc/Anti-corrosive Coating
- Packaging: Bundled/in Bulk, Plastic Caps Plugged, Waterproof Paper Wrapped For details,deliver time and prices, please mail us.
Seamless Steel Pipe
Seamless steel pipes are made from high-quality steel, typically processed through hot rolling or cold drawing methods. They are known for their uniform structure, precise dimensions, and excellent mechanical properties, making them suitable for high-pressure applications. These pipes have a smooth interior surface, which reduces friction and allows for efficient flow of fluids or gases. Seamless steel pipes are widely used in the oil and gas industry for drilling, pipelines, and transportation of fluids under high pressure. They are also essential in construction for structural support and in the water and energy sectors for conveying fluids. Other applications include automotive, shipbuilding, and manufacturing industries where reliability and resistance to environmental factors are critical.
Production Process
Mandrel Mill Process:
In the Mandrel Mill Process, a solid round billet is used. It is heated in a rotary hearth furnace and then pierced by a piercer. The resulting hollow shell is rolled by a mandrel mill to reduce its outside diameter and wall thickness, forming a multiple-length mother tube. This mother tube is reheated and further reduced to specified dimensions by a stretch reducer. Afterward, the tube is cooled, cut, straightened, and subjected to finishing and inspection processes before being shipped.
Mannesmann plug mill process:
In the Plug Mill Process, a solid round billet is used. It is uniformly heated in a rotary hearth furnace and then pierced by a Mannesmann piercer. The pierced billet, now a hollow shell, undergoes rolling to reduce its outside diameter and wall thickness. The rolled tube is simultaneously burnished inside and outside by a reeling machine. Next, a sizing mill sizes the tube to the specified dimensions. The tube then passes through a straightener, completing the hot working process. After finishing and inspection, the tube, now referred to as a mother tube, becomes the finished product.
Specification
Specification of Seamless steel pipe
This specification pertains to seamless and welded carbon and alloy steel pipes designed for use at low temperatures. The pipes should be produced through seamless or welding processes without the addition of filler metal during welding. All seamless and welded pipes must undergo treatment to control their microstructure. Tensile tests, impact tests, hydrostatic tests, and nondestructive electric tests must be conducted in accordance with specified requirements.
NOMINAL PT PF SIZE | OUTSIDE DIAMETER | NOMINAL WALL THICKNESS | |||||||||||||||||
A | B | ASME | JIS | DIN | JIS(l) | DIN (2) | SCH10 | SCH20 | SCH30 | STD | SCH40 | SCH60 | XS | SCH80 | SCH100 | SCH120 | SCH140 | SCH160 | XXS |
15 | 1/2″ | 21.3 | 21.7 | 21.3 | 2.8 | 2.0 | 2. 11 | 2.41 | 2.77 | 3.73 | 3.73 | 4.78 | 7.47 | ||||||
20 | 3/4″ | 26.7 | 27.2 | 26.9 | 2.8 | 2.3 | 2. 11 | 2.41 | 2.87 | 2.87 | 3.91 | 3.91 | 5.56 | 7.82 | |||||
25 | 1″ | 33.4 | 34.0 | 33.7 | 3.2 | 2.6 | 2.77 | 2.90 | 3.38 | 3.38 | 4.55 | 4.55 | 6.35 | 9.09 | |||||
32 | 1.1/4″ | 42.2 | 42.7 | 42.4 | 3.5 | 2.6 | 2.77 | 2.97 | 3.56 | 3.56 | 4.85 | 4.85 | 6.35 | 9.70 | |||||
40 | 1. 1/2″ | 48.3 | 48.6 | 48.3 | 3.5 | 2.6 | 2.77 | 3. 18 | 3.68 | 3.68 | 5.08 | 5.08 | 7. 14 | 10. 15 | |||||
50 | 2″ | 60.3 | 60.5 | 60.3 | 3.8 | 2.9 | 2.77 | 3. 18 | 3.91 | 3.91 | 5.54 | 5.54 | 8.74 | 11.07 | |||||
65 | 2. 1/2″ | 73.0 | 76.3 | 76. 1 | 4.2 | 2.9 | 3.05 | 4.78 | 5.16 | 5. 16 | 7.01 | 7.01 | 9.53 | 14.02 | |||||
80 | 3″ | 88.9 | 89. 1 | 88.9 | 4.2 | 3.2 | 3.05 | 4.78 | 5.49 | 5.49 | 7.62 | 7.62 | 11. 13 | 15.24 | |||||
90 | 3. 1/2″ | 101.6 | 101.6 | 4.2 | 3.05 | 4.78 | 5.74 | 5.74 | 8.08 | 8.08 | |||||||||
100 | 4″ | 114.3 | 114.3 | 114.3 | 4.5 | 3.6 | 3.05 | 4.78 | 6.02 | 6.02 | 8.56 | 8.56 | 11. 13 | 13.49 | 17. 12 | ||||
125 | 5″ | 141.3 | 139.8 | 139.7 | 4.5 | 4.0 | 3.40 | 6.55 | 6.55 | 9.53 | 9.53 | 12.70 | 15.88 | 19.05 | |||||
150 | 6″ | 168.3 | 165.2 | 168.3 | 5.0 | 4.5 | 3.40 | 4.50 | 7.11 | 7. 11 | 10.97 | 10.97 | 14.27 | 18.26 | 21.95 | ||||
200 | 8″ | 219. 1 | 216.3 | 219. 1 | 5.8 | 6.3 | 3.76 | 6.35 | 7.04 | 8.18 | 8. 18 | 10.31 | 12.70 | 12.70 | 15.09 | 18.26 | 20.62 | 23.01 | 22.23 |
250 | 10″ | 273.0 | 267.4 | 273.0 | 6.6 | 6.3 | 4. 19 | 6.35 | 7.80 | 9.27 | 9.27 | 12.70 | 12.70 | 15.09 | 18.26 | 21.44 | 25.40 | 28.58 | 25.40 |
300 | 12″ | 323.8 | 318.5 | 323.9 | 6.9 | 7. 1 | 4.57 | 6.35 | 8.38 | 9.53 | 10.31 | 14.27 | 12.70 | 17.48 | 21.44 | 25.40 | 28.58 | 33.32 | 25.40 |
350 | 14″ | 355.6 | 355.6 | 355.6 | 7.9 | 8.0 | 6.35 | 7.92 | 9.53 | 9.53 | 11. 13 | 15.09 | 12.70 | 19.05 | 23.83 | 27.79 | 31.75 | 35.71 | |
400 | 16″ | 406.4 | 406.4 | 406.4 | 7.9 | 8.8 | 6.35 | 7.92 | 9.53 | 9.53 | 12.70 | 16.66 | 12.70 | 21.44 | 26. 19 | 30.96 | 36.53 | 40.49 | |
450 | 18″ | 457.2 | 457.2 | 457.0 | 7.9 | 10.0 | 6.35 | 7.92 | 11. 13 | 9.53 | 14.27 | 19.05 | 12.70 | 23.83 | 29.36 | 34.93 | 39.67 | 45.24 | |
500 | 20″ | 508.0 | 508.0 | 508.0 | 7.9 | 11.0 | 6.35 | 9.53 | 12.70 | 9.53 | 15.09 | 20.62 | 12.70 | 26. 19 | 32.54 | 38. 10 | 44.45 | 50.01 | |
550 | 22″ | 558.8 | 558.8 | 6.35 | 9.53 | 12.70 | 9.53 | 22.23 | 12.70 | 28.58 | 34.93 | 41.28 | 47.63 | 53.98 | |||||
600 | 24″ | 609.6 | 609.6 | 610.0 | 12.5 | 6.35 | 9.53 | 14.27 | 9.53 | 17.48 | 24.61 | 12.70 | 30.96 | 38.89 | 46.02 | 52.37 | 59.54 | ||
650 | 26″ | 660.4 | 660.4 | 7.92 | 12.70 | 9.53 | 12.70 | ||||||||||||
700 | 28″ | 711.2 | 711.2 | 711.0 | 12.5 | 7.92 | 12.70 | 15.88 | 9.53 | 12.70 | |||||||||
750 | 30″ | 762.0 | 762.0 | 7.92 | 12.70 | 15.88 | 9.53 | 12.70 | |||||||||||
800 | 32″ | 812.8 | 812.8 | 813.0 | 12.5 | 7.92 | 12.70 | 15.88 | 9.53 | 17.48 | 12.70 | ||||||||
850 | 34″ | 863.6 | 863.6 | 7.92 | 12.70 | 15.88 | 9.53 | 17.48 | 12.70 | JIS | G3452 ASME B36.10M | ||||||||
900 | 36″ | 914.4 | 914.4 | 914.0 | 12.5 | 7.92 | 12.70 | 15.88 | 9.53 | 19.05 | 12.70 | JIS | G3454 DIN2448 | ||||||
950 | 38″ | 965.2 | 965.2 | 9.53 | 12.70 | JIS | G3455 DIN2458 | ||||||||||||
1000 | 40″ | 1016. 0 | 1016. 0 | 1016. 0 | 12. 5 | 9.53 | 12. 70 | JIS | G3457 | ||||||||||
1050 | 42″ | 1066.8 | 1066.8 | 9.53 | 12.70 | ||||||||||||||
1100 | 44″ | 1117.6 | 1117.6 | 9.53 | 12.70 | ||||||||||||||
1150 | 46″ | 1168.4 | 1168.4 | 9.53 | 12.70 | ||||||||||||||
1200 | 48″ | 1219.2 | 1219.2 | 1220.0 | 9.53 | 12.70 |
Technical Data
Seamless Steel Pipe Chemical Composition and Mechanical Properties
This data provides a brief summary of the referenced standard. It is for informational purposes only and is not an official part of the standard. For its use and application, the full text of the standard itself must be consulted. ASTM does not offer any warranty, express or implied, nor does it make any representation that the contents of this abstract are accurate, complete, or up to date.
Standard | Grade | Chemical Composition (%) | Mechanical Properties | |||||
ASTM A53 | C | Si | Mn | P | S | Tensile STrength(Mpa) | Yield STrength(Mpa) | |
A | ≤0.25 | – | ≤0.95 | ≤0.05 | ≤0.06 | ≥330 | ≥205 | |
B | ≤0.30 | – | ≤1.2 | ≤0.05 | ≤0.06 | ≥415 | ≥240 | |
ASTM A106 | A | ≤0.30 | ≥0.10 | 0.29-1.06 | ≤0.035 | ≤0.035 | ≥415 | ≥240 |
B | ≤0.35 | ≥0.10 | 0.29-1.06 | ≤0.035 | ≤0.035 | ≥485 | ≥275 | |
ASTM A179 | A179 | 0.06-0.18 | – | 0.27-0.63 | ≤0.035 | ≤0.035 | ≥325 | ≥180 |
ASTM A192 | A192 | 0.06-0.18 | ≤0.25 | 0.27-0.63 | ≤0.035 | ≤0.035 | ≥325 | ≥180 |
API 5L PSL1 | A | 0.22 | – | 0.90 | 0.030 | 0.030 | ≥331 | ≥207 |
B | 0.28 | – | 1.20 | 0.030 | 0.030 | ≥414 | ≥241 | |
X42 | 0.28 | – | 1.30 | 0.030 | 0.030 | ≥414 | ≥290 | |
X46 | 0.28 | – | 1.40 | 0.030 | 0.030 | ≥434 | ≥317 | |
X52 | 0.28 | – | 1.40 | 0.030 | 0.030 | ≥455 | ≥359 | |
X56 | 0.28 | – | 1.40 | 0.030 | 0.030 | ≥490 | ≥386 | |
X60 | 0.28 | – | 1.40 | 0.030 | 0.030 | ≥517 | ≥448 | |
X65 | 0.28 | – | 1.40 | 0.030 | 0.030 | ≥531 | ≥448 | |
X70 | 0.28 | – | 1.40 | 0.030 | 0.030 | ≥565 | ≥483 | |
API 5L PSL2 | B | 0.24 | – | 1.20 | 0.025 | 0.015 | ≥414 | ≥241 |
X42 | 0.24 | – | 1.30 | 0.025 | 0.015 | ≥414 | ≥290 | |
X46 | 0.24 | – | 1.40 | 0.025 | 0.015 | ≥434 | ≥317 | |
X52 | 0.24 | – | 1.40 | 0.025 | 0.015 | ≥455 | ≥359 | |
X56 | 0.24 | – | 1.40 | 0.025 | 0.015 | ≥490 | ≥386 | |
X60 | 0.24 | – | 1.40 | 0.025 | 0.015 | ≥517 | ≥414 | |
X65 | 0.24 | – | 1.40 | 0.025 | 0.015 | ≥531 | ≥448 | |
X70 | 0.24 | – | 1.40 | 0.025 | 0.015 | ≥565 | ≥483 | |
X80 | 0.24 | – | 1.40 | 0.025 | 0.015 | ≥621 | ≥552 |
Carbon Steel Seamless Pipe Composition and Mechanical Properties
Standard | Grade | Chemical Composition | Mechanical Properties | |||||||||
C | Si | Mn | P | S | Cr | Ni | Cu | Tensile Strength(Mpa) | Yield Strength(Mpa) | Elongation(%) | ||
GB/T8163 | 10 | 0.07- 0.14 | 0.17- 0.37 | 0.35- 0.65 | ≤0.035 | ≤0.035 | ≤0.15 | ≤0.25 | ≤0.25 | 335-457 | ≥205 | ≥24 |
20 | 0.17- 0.24 | 0.17- 0.37 | 0.35- 0.65 | ≤0.035 | ≤0.035 | ≤0.25 | ≤0.25 | ≤0.25 | 410-550 | ≥245 | ≥20 | |
Q345 | 0.12- 0.20 | 0.20- 0.55 | 1.20- 1.60 | ≤0.045 | ≤0.045 | – | – | – | 490-665 | ≥325 | ≥21 |
Carbon Steel Seamless Pipe Tolerance
Pipe types | Pipe Szie(mm) | Tolerances | |
Hot rolled | OD | All | ±1% (min ±0.50mm) |
WT | All | ±15%, -12.5% | |
Cold drawn | OD | 6-10 | ±0.20mm |
10-30 | ±0.40mm | ||
30-50 | ±0.45mm | ||
>50 | ±1% | ||
WT | ≤1 | +0.15mm | |
>1-3 | +15% -10% | ||
>3 | +12.5% -10% |
Seamless Steel Pipe End
Plain End | Wall Thickness less than 0.5 inch, including SCH STD & SCH XS | |||||
Plain End (Square Cut) | Wall Thickness over 0.5 inch, including SCH XXS | |||||
Beveled End | Wall Thickness less than 0.5 inch, including SCH STD & SCH XS | |||||
Couplings | Outside Diameter equal or less than 2″ | |||||
Thread Protection | Outside Diameter over 4 inch |
Surface
Surface treatment significantly impacts the longevity of the coating, playing a crucial role in determining the lifespan of the pipe coating. To extend the life of seamless steel pipes, surface treatment is essential and should be continuously improved.
Surface strength seamless steel pipe, the surface roughness of the original rust into a degree, abrasive coating material to choose, in order to achieve better results, as well as the role of grit etched steel surface, has strengthened steel shot the role of steel surface, mixing abrasive steel shot and grit, for it can be a single layer of epoxy easier to achieve the desired effect.
Before applying a coating to seamless tubes, it’s crucial to pre-treat the outer wall surface to address any rust. This involves thoroughly cleaning the outer surface to remove grease, dirt, and debris, ensuring both inner and outer walls have a smooth surface. After clearing the inner and outer walls, any rust or iron oxide on the outer surface must be manually removed to meet grade standards. Once rust removal is confirmed through inspection, a primer should be applied within 8 hours. In adverse atmospheric conditions, such as high humidity or air containing salt spray, this time frame should be shortened. When applying corrosion-resistant paint to the pipeline, the nature of the paint should dictate the preparation process. The paint should be properly mixed and applied to the pipe surface using a brush with an appropriate level of softness. Brushing should be uniform, avoiding excessive buildup or leakage. The application of anti-corrosion coating paint should be divided into sections, ensuring each section is painted before the previous one dries to maintain consistency.
Excessive abrasive roughness can result in a thin coating, as a deep anchor pattern may cause bubbles to form during the corrosion process, significantly compromising coating performance. Conversely, if the roughness is too minimal, it can diminish coating impact strength and adhesion. Utilizing small particles for polishing to remove corrosion products aims to enhance abrasive efficiency while mitigating wear on pipes and nozzles.
Packaging:
Packaged either in bundles or in bulk, the ends are sealed with plastic caps and wrapped in waterproof paper.
Product Advantages of Seamless Steel Pipe
1) The primary benefit of seamless steel pipes lies in their enhanced capacity to endure pressure. Unlike welded steel pipes, which have their weakest point at the welded seam, seamless steel pipes lack this seam altogether, rendering them uniformly strong throughout their entire circumference.
2) The nature of wrapping welded seam pipe around another form before welding, coupled with the introduction of heat, stress, and other variables during the welding process, prevents it from achieving the same level of roundness as seamless steel pipe.
3) While seamless steel pipe may occasionally carry a higher price tag compared to other types of steel pipe, its reliability surpasses that of alternatives.
Other
Seamless Steel Pipe Classification and Application
Types | Application |
Structure Purposes | General structure and mechanical |
Liquid Services | Petroleum, gas and other fluids conveying |
Low and Medium Pressure | Steam and boiler manufacturing |
Hydraulic Pillar Service | Hydraulic support |
Auto Semi-shaft Casing | Auto sem-shaft casing |
Line Pipe | Oil and gas conveying |
Tubing and Casing | Oil and gas conveying |
Drill Pipes | Well drilling |
Geological Drilling Pipe | Geological drilling |
Petroleum Cracking Tubes | Furnace tubes, heat exchangers |