Introduction
In the world of construction, material selection is crucial for ensuring the durability, safety, and efficiency of any project. Among the various materials available, seamless mechanical tubing stands out due to its superior strength, versatility, and reliability. This comprehensive guide will explore the benefits of using seamless mechanical tubing in construction, highlighting its unique properties and applications.
Understanding Seamless Mechanical Tubing
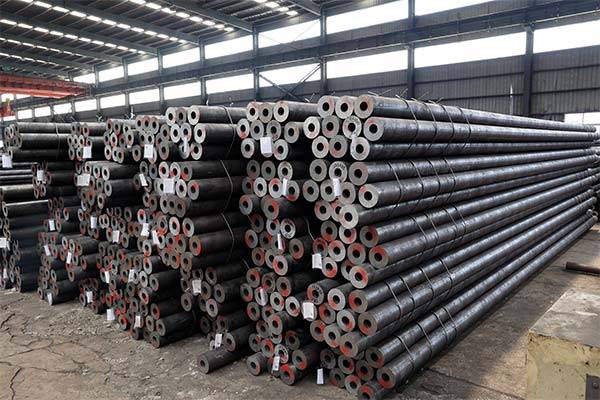
What is Seamless Mechanical Tubing?
Seamless mechanical tubing is a type of tubing made from solid steel that is heated and extruded to create a hollow tube. Unlike welded tubing, seamless tubing does not have a seam or weld line, which gives it enhanced strength and durability.
Key Features
- No Weld Seam: Provides uniform strength and reduces the risk of failure.
- High Strength: Ideal for heavy-duty applications.
- Precision Dimensions: Ensures accurate and consistent sizing.
How is Seamless Mechanical Tubing Manufactured?
The manufacturing process of seamless mechanical tubing involves several steps:
Billet Preparation: Solid steel billets are cut to the desired length.
Heating: The billets are heated to a high temperature to make them malleable.
Piercing: The heated billet is pierced with a mandrel to create a hollow tube.
Extrusion: The hollow billet is extruded through a die to achieve the desired diameter and wall thickness.
Finishing: The tubing is cooled, straightened, and cut to length.
Benefits of Seamless Mechanical Tubing in Construction
Superior Strength and Durability
One of the primary benefits of seamless mechanical tubing is its superior strength. The absence of a weld seam means there are no weak points, making it less prone to failure under stress. This characteristic is particularly important in construction, where materials are subjected to heavy loads and harsh conditions.
Applications
- Structural Supports: Beams, columns, and frameworks.
- Heavy Machinery: Components that require high strength and durability.
- Infrastructure Projects: Bridges, tunnels, and highways.
Enhanced Safety
Seamless mechanical tubing’s uniform strength and high load-bearing capacity contribute to enhanced safety in construction projects. The reliability of the material reduces the risk of structural failures, which can lead to accidents and costly repairs.
Safety Benefits
- Consistent Performance: Reduces the likelihood of unexpected failures.
- High Load Capacity: Supports greater weights without compromising stability.
- Resistant to Environmental Factors: Withstands corrosion, temperature fluctuations, and impact.
Versatility and Flexibility
Seamless mechanical tubing is available in various sizes, thicknesses, and grades, making it suitable for a wide range of applications. Its versatility allows it to be used in both standard and custom construction projects.
Applications
- Piping Systems: Water, gas, and oil pipelines.
- Architectural Elements: Handrails, staircases, and decorative features.
- Mechanical Components: Shafts, cylinders, and rollers.
Cost-Effectiveness
While seamless mechanical tubing may have a higher initial cost compared to welded tubing, its durability and low maintenance requirements make it a cost-effective choice in the long run. The reduced risk of failure and the need for fewer repairs translate into significant savings over the life of a project.
Cost Benefits
- Reduced Maintenance: Fewer repairs and replacements needed.
- Longer Lifespan: Higher durability extends the service life of structures.
- Lower Risk of Downtime: Enhanced reliability minimizes project delays.
Precision and Quality
The manufacturing process of seamless mechanical tubing ensures precise dimensions and high-quality finishes. This precision is crucial in construction, where accurate measurements are necessary for fitting and alignment.
Quality Benefits
- Tight Tolerances: Ensures consistent performance and compatibility.
- Smooth Finish: Reduces friction and wear in mechanical applications.
- High-Quality Material: Enhances the overall integrity of construction projects.
Table: Comparison of Seamless Mechanical Tubing and Welded Tubing
Property | Seamless Mechanical Tubing | Welded Tubing |
---|---|---|
Strength | High (no weld seam) | Moderate (potential weak points) |
Durability | Excellent | Good |
Precision | High | Variable |
Cost | Higher initial cost | Lower initial cost |
Applications | Heavy-duty, high-stress environments | General construction, low-stress applications |
Manufacturing Process | Extrusion and piercing | Welding and forming |
Maintenance Requirements | Low | Moderate to high |
Load-Bearing Capacity | High | Variable |
Key Applications of Seamless Mechanical Tubing in Construction
Structural Applications
Seamless mechanical tubing is widely used in structural applications due to its high strength and reliability. It is ideal for constructing frameworks, beams, and columns that need to support significant loads.
Examples
- Building Frameworks: Provides structural integrity for commercial and residential buildings.
- Bridges: Used in the construction of bridge supports and trusses.
- Towers: Essential for the stability of communication and transmission towers.
Piping and Plumbing Systems
The precision and durability of seamless mechanical tubing make it an excellent choice for piping and plumbing systems. It is commonly used in water, gas, and oil pipelines due to its ability to withstand high pressures and resist corrosion.
Examples
- Water Supply Systems: Ensures clean and safe delivery of water.
- Gas Pipelines: Safe transport of natural gas and other gases.
- Oil Pipelines: Efficiently transports crude oil and refined products.
Mechanical and Industrial Components
Seamless mechanical tubing is also used in the manufacturing of various mechanical and industrial components. Its high precision and quality make it suitable for applications requiring tight tolerances and high performance.
Examples
- Hydraulic Cylinders: Provides smooth and reliable operation.
- Rollers and Shafts: Essential for machinery and equipment.
- Bearings: Reduces friction and wear in moving parts.
Architectural Elements
Architects and designers use seamless mechanical tubing for creating aesthetic and functional elements in buildings. Its versatility allows for the construction of sleek and modern designs.
Examples
- Handrails and Railings: Provides safety and aesthetics in staircases and balconies.
- Structural Glass Supports: Ensures stability and transparency in glass structures.
- Decorative Features: Adds unique design elements to buildings and structures.
Maintenance and Care of Seamless Mechanical Tubing
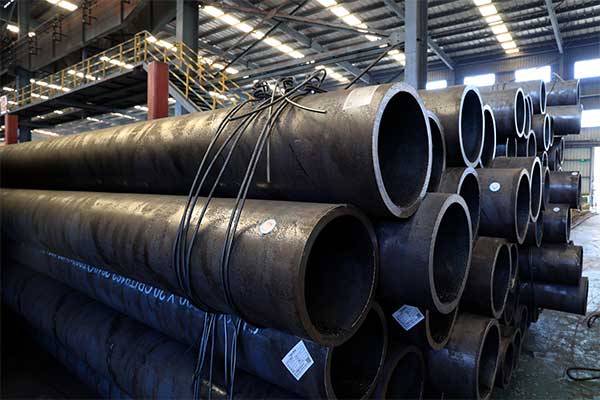
Regular Inspections
Conduct regular inspections to identify any signs of wear, corrosion, or damage. Early detection of issues can prevent costly repairs and ensure the longevity of the tubing.
Inspection Tips
- Visual Checks: Look for cracks, rust, and other visible damage.
- Ultrasonic Testing: Detects internal defects that are not visible to the naked eye.
- Pressure Testing: Ensures the tubing can handle operational pressures.
Proper Handling and Installation
Ensure that seamless mechanical tubing is handled and installed correctly to avoid damage and ensure optimal performance. Follow manufacturer guidelines and industry best practices.
Handling Tips
- Avoid Dropping: Dropping the tubing can cause dents and cracks.
- Use Proper Tools: Use tools designed for handling and cutting metal tubing.
- Secure Installation: Ensure all connections are tight and secure.
Protective Coatings and Treatments
Applying protective coatings or treatments can enhance the durability and lifespan of seamless mechanical tubing. These treatments can provide additional resistance to corrosion and wear.
Common Treatments
- Galvanization: Coating with zinc to prevent rust.
- Powder Coating: Provides a durable and attractive finish.
- Anodizing: Increases corrosion resistance and surface hardness.
Conclusion
Seamless mechanical tubing offers numerous benefits for construction projects, including superior strength, enhanced safety, versatility, cost-effectiveness, and precision. Its wide range of applications, from structural supports to piping systems and architectural elements, makes it an indispensable material in the construction industry. By understanding the advantages of seamless mechanical tubing and selecting the right type for your project, you can ensure durability, reliability, and efficiency in your construction endeavors.
FAQ
What is the main advantage of seamless mechanical tubing over welded tubing?
The main advantage of seamless mechanical tubing is its superior strength and durability. The absence of a weld seam eliminates potential weak points, making it more reliable for high-stress and heavy-duty applications.
Can seamless mechanical tubing be used for both structural and mechanical applications?
Yes, seamless mechanical tubing is versatile and can be used for both structural and mechanical applications. Its high strength, precision dimensions, and durability make it suitable for a wide range of uses.
How does the cost of seamless mechanical tubing compare to welded tubing?
Seamless mechanical tubing generally has a higher initial cost compared to welded tubing. However, its long-term durability, lower maintenance requirements, and reduced risk of failure can make it a more cost-effective choice over the lifespan of a project.
What types of protective coatings can be applied to seamless mechanical tubing?
Common protective coatings for seamless mechanical tubing include galvanization (zinc coating), powder coating, and anodizing. These treatments enhance corrosion resistance, durability, and surface hardness.
How often should seamless mechanical tubing be inspected and maintained?
Regular inspections should be conducted based on the operational environment and usage. Visual checks, ultrasonic testing, and pressure testing can help identify potential issues early. Maintenance should include proper handling, secure installation, and the application of protective coatings to ensure longevity.