Welcome to My Blog!
Before we dive into the content, I’d love for you to join me on my social media platforms where I share more insights, engage with the community, and post updates. Here’s how you can connect with me:
Facebook:https://www.facebook.com/profile.php?id=61559060896490
Now, let’s get started on our journey together. I hope you find the content here insightful, engaging, and valuable.
Table of Contents
Introduction
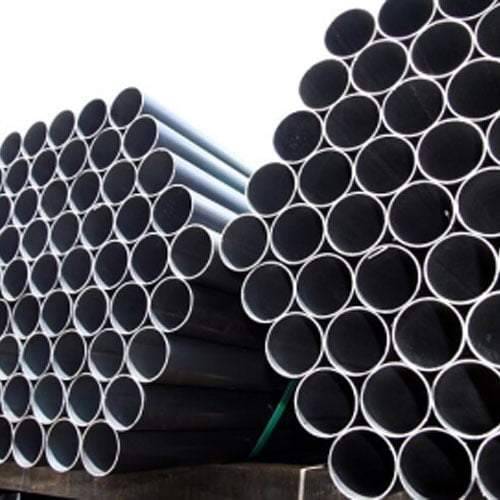
Boiler steel tubes are indispensable components in various industrial applications, primarily serving as the backbone of boiler systems. These tubes are subjected to extreme operating conditions, including high temperatures, pressures, and corrosive environments. As a result, they must possess exceptional mechanical properties, such as high strength, durability, and resistance to corrosion.
This blog post will delve into the diverse applications of boiler steel tubes across various industries. We will explore the different types of boiler steel tubes, their manufacturing processes, and the critical factors to consider when selecting the appropriate tube for a specific application. We will also discuss the factors influencing the lifespan of boiler tubes and provide insights into maintenance practices to ensure optimal performance.
The Role of Boiler Steel Tubes in Industrial Processes
Boiler steel tubes play a pivotal role in industrial processes by efficiently transferring heat from the combustion chamber to the working fluid. They are designed to withstand the high pressures generated within the boiler system, ensuring safe and reliable operation. Additionally, these tubes are engineered to resist corrosion, extending their lifespan and minimizing maintenance requirements.
Types of Boiler Steel Tubes
Boiler steel tubes are categorized based on their composition, manufacturing process, and intended use. Common types include:
- Carbon steel tubes: These tubes offer a good balance of strength and cost-effectiveness, making them suitable for general-purpose boiler applications. However, they may be susceptible to corrosion in harsh environments.
- Alloy steel tubes: Containing alloying elements like chromium, molybdenum, and vanadium, these tubes exhibit enhanced corrosion resistance and high-temperature strength. They are commonly used in high-pressure and high-temperature applications, such as superheaters and reheaters.
- Stainless steel tubes: Highly resistant to corrosion and oxidation, stainless steel tubes are ideal for applications involving corrosive fluids or high-temperature environments. They are commonly used in food processing, chemical processing, and marine industries.
Manufacturing Processes
Boiler steel tubes are produced through various manufacturing processes, including:
- Hot rolling: This process involves heating a steel billet to a high temperature and then rolling it into a tubular shape. Hot rolling is commonly used to produce large-diameter tubes.
- Cold drawing: Cold drawing involves pulling a hot-rolled tube through a die to reduce its diameter and improve its surface finish. Cold drawing is used to produce tubes with precise dimensions and enhanced mechanical properties.
- Welding: Welded tubes are produced by joining two steel plates or strips together using a welding process. Seamless tubes, on the other hand, are produced without any welds, offering superior strength and durability.
Selection Criteria for Boiler Steel Tubes
When selecting boiler tubes, several factors must be considered to ensure optimal performance and longevity:
- Operating conditions: The temperature, pressure, and corrosive environment of the application will dictate the required material properties.
- Material compatibility: The tube material must be compatible with the working fluid and other system components to avoid corrosion and degradation.
- Mechanical properties: The tube must possess sufficient strength, ductility, and fatigue resistance to withstand the operating conditions.
- Cost: The cost of the tube material and manufacturing process must be balanced with performance requirements and budgetary constraints.
Applications of Boiler Steel Tubes in Various Industries
Boiler steel tubes find widespread applications in numerous industries, including:
- Power generation: Used in boilers to produce steam for driving turbines, powering electricity generation plants.
- Chemical processing: Employed in heat exchangers, reactors, and pipelines to transport and process various chemicals.
- Petroleum refining: Utilized in furnaces, heat recovery units, and distillation columns in refineries.
- Pulp and paper: Used in paper machines, recovery boilers, and digesters in the pulp and paper industry.
- Food processing: Employed in sterilizers, evaporators, and heat exchangers in the food processing industry.
- Marine industry: Used in boilers, heat exchangers, and piping systems in ships and offshore platforms.
Comparison of Boiler Steel Tube Materials
Material | Advantages | Disadvantages | Typical Applications |
---|---|---|---|
Carbon steel | Cost-effective, good strength | Susceptible to corrosion | General-purpose boilers, low-pressure applications |
Alloy steel | High strength, corrosion resistance, creep resistance | Higher cost | High-temperature, high-pressure applications, superheaters, reheaters |
Stainless steel | Excellent corrosion resistance, high-temperature strength | Higher cost | Corrosive environments, food processing, chemical processing, marine industry |
Factors Affecting the Lifespan of Boiler Steel Tubes
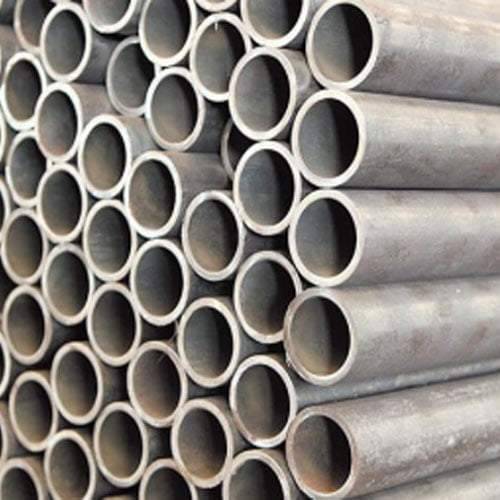
The lifespan of boiler steel tubes is influenced by several factors:
- Material quality: The composition and manufacturing process of the tube significantly impact its lifespan. High-quality materials with proper manufacturing techniques can extend the tube’s life.
- Operating conditions: The temperature, pressure, and corrosive environment of the application can accelerate or decelerate the degradation of the tube.
- Maintenance practices: Regular inspection, cleaning, and repair of boiler tubes can help prevent premature failure and extend their lifespan.
Conclusion
Boiler steel tubes are essential components in various industrial applications, playing a critical role in heat transfer, pressure containment, and corrosion resistance. By understanding the different types of boiler steel tubes, their manufacturing processes, and the factors influencing their selection, engineers and designers can choose the most suitable tube for their specific application.
Proper maintenance and inspection practices are crucial to ensure the longevity and reliability of boiler tubes. By implementing effective maintenance strategies, industries can optimize the performance of their boiler systems and minimize downtime.
FAQ
What are the primary factors affecting the lifespan of a boiler steel tube?
The primary factors affecting the lifespan of a boiler steel tube include operating conditions (temperature, pressure, and corrosive environment), material quality, and maintenance practices.
How do I select the right boiler tube for my application?
To select the right boiler tube, consider factors such as the operating conditions, required mechanical properties, corrosion resistance, and cost. Consult with a materials engineer or supplier to determine the best choice.
What are the common applications of boiler steel tubes in the power generation industry?
Boiler steel tubes are widely used in power generation for various components, including boiler tubes, superheater tubes, reheater tubes, and economizer tubes. They play a crucial role in efficiently transferring heat from the combustion chamber to the working fluid.
What are the differences between carbon steel and stainless steel tubes?
Carbon steel tubes are more cost-effective but are susceptible to corrosion. Stainless steel tubes, on the other hand, offer superior corrosion resistance but are more expensive. The choice between the two depends on the specific application and its operating conditions.
How can I improve the efficiency of heat transfer in a boiler system using boiler steel tubes?
To improve heat transfer efficiency, consider factors such as tube material, tube geometry, and surface condition. Proper maintenance, cleaning, and optimization of the boiler system can also enhance heat transfer.