Welcome to My Blog!
Before we dive into the content, I’d love for you to join me on my social media platforms where I share more insights, engage with the community, and post updates. Here’s how you can connect with me:
Facebook:https://www.facebook.com/profile.php?id=61559060896490
Now, let’s get started on our journey together. I hope you find the content here insightful, engaging, and valuable.
Table of Contents
Introduction
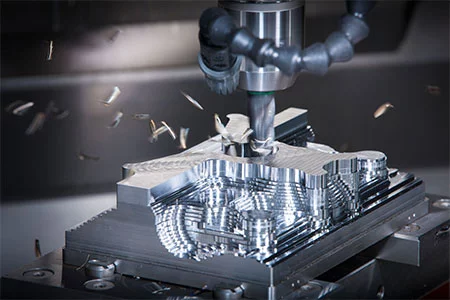
Selecting the right stainless steel material for your project is crucial to ensuring not only durability but also aesthetics and overall performance. Stainless steel is a widely used material known for its exceptional properties, such as corrosion resistance, strength, and versatility, which make it a popular choice across various industries, including construction, automotive, and food processing. Its ability to withstand harsh environments and resist tarnishing sets it apart from other materials, allowing it to maintain its integrity and appearance over time.
However, despite the many advantages that stainless steel offers, many individuals and companies fall into common traps when choosing the appropriate stainless steel materials. These mistakes can lead to unexpected costs, project delays, and compromised quality, ultimately affecting the success of the entire endeavor.
In this comprehensive article, we will delve into the five most significant mistakes to avoid when selecting stainless steel material for your projects. By understanding these pitfalls, you will be better equipped to make informed decisions that enhance the efficiency, durability, and success of your projects. This knowledge will not only save you time and resources but also contribute to the longevity and reliability of your finished products. Let’s explore these mistakes in detail to ensure that your next stainless steel selection process is smooth and successful.
Understanding Stainless Steel Material
Before delving into the mistakes, it’s essential to understand the different types and grades of stainless steel material available in the market. Stainless steel is primarily classified into three categories: austenitic, ferritic, and martensitic, each with unique properties and applications.
Austenitic Stainless Steel
Austenitic stainless steel is the most widely used type, known for its excellent corrosion resistance, weldability, and formability. Common grades include 304 and 316, which are often used in food processing, kitchen equipment, and chemical applications.
Ferritic Stainless Steel
Ferritic stainless steel contains less nickel than austenitic types and offers good corrosion resistance and high-temperature strength. However, it is less ductile and not suitable for welding. Grades like 430 are commonly used in automotive and appliance applications.
Martensitic Stainless Steel
Martensitic stainless steel is characterized by high strength and hardness, making it suitable for applications requiring strength, such as cutlery and surgical instruments. Common grades include 410 and 420.
Mistake 1: Ignoring the Grade of Stainless Steel Material
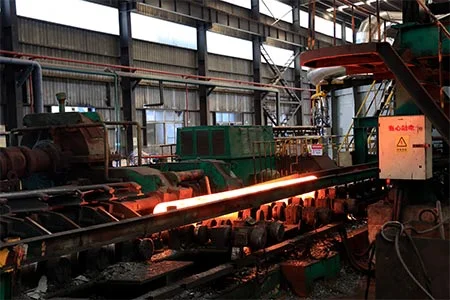
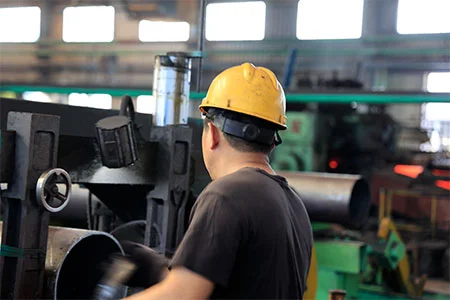
One of the most critical mistakes when choosing stainless steel material is overlooking the specific grade required for your project. Each grade has distinct properties, and selecting the wrong one can lead to poor performance and premature failure.
Key Considerations
- Corrosion Resistance: If your application involves exposure to corrosive environments, select a grade with high corrosion resistance, such as 316 stainless steel.
- Mechanical Properties: Understand the mechanical properties required for your application, including strength, hardness, and ductility.
Mistake 2: Underestimating the Importance of Surface Finish
The surface finish of stainless steel material can significantly impact its appearance, performance, and resistance to corrosion. Many people fail to consider this aspect, resulting in unsuitable finishes for their applications.
Common Surface Finishes
Finish Type | Description | Applications |
---|---|---|
2B | A smooth, reflective finish created by cold rolling. | Food processing, kitchen equipment |
No. 4 | A brushed finish that reduces visibility of scratches. | Appliances, architectural applications |
Mirror | A highly reflective finish achieved through polishing. | Decorative applications, luxury products |
Choosing the appropriate surface finish can enhance the material’s durability and aesthetic appeal while reducing maintenance needs.
Mistake 3: Failing to Consider Environmental Factors
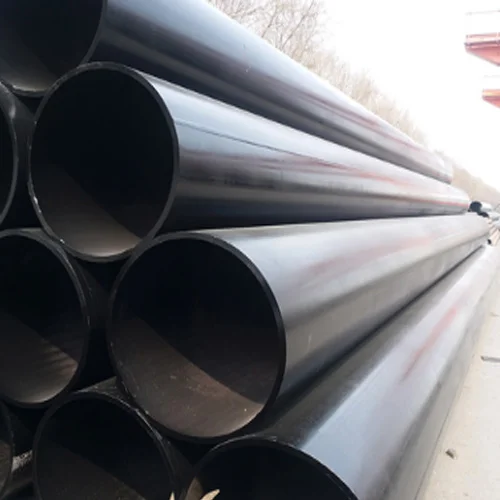
The environment in which the stainless steel material will be used plays a crucial role in determining its suitability for specific applications. Many individuals and project managers neglect to thoroughly assess the environmental factors that can significantly affect the performance and longevity of stainless steel, leading to costly mistakes that could have been easily avoided.
Key Environmental Considerations
Exposure to Chemicals:
One of the most critical aspects to consider is the potential exposure of stainless steel to various chemicals. Different grades of stainless steel exhibit varying levels of resistance to corrosive substances. For instance, if the stainless steel will be used in environments where it may come into contact with acids, alkalis, or other harsh chemicals, it is essential to ensure that the selected grade is specifically designed to resist those specific substances.
For example, grade 316 stainless steel is well-known for its superior resistance to corrosion from chlorides and other aggressive agents, making it an ideal choice for marine environments or chemical processing applications. Neglecting to consider the chemical exposure can lead to rapid deterioration, compromised structural integrity, and ultimately costly repairs or replacements.
Temperature Extremes:
Another significant factor to consider is the temperature range in which the stainless steel material will operate. Various grades of stainless steel have different thermal properties, and some may lose strength or become brittle when exposed to extreme temperatures, whether high or low. For example, austenitic stainless steels like 304 and 316 retain their toughness at low temperatures, making them suitable for cryogenic applications. Conversely, certain grades may become less ductile at elevated temperatures, potentially leading to failure under stress. Understanding the temperature extremes your stainless steel will face and selecting an appropriate grade is essential for ensuring reliable performance and longevity, particularly in industries such as aerospace, automotive, and industrial manufacturing.
By carefully evaluating these environmental factors, you can avoid the pitfalls associated with inappropriate material selection and ensure that your stainless steel components will perform optimally in their intended applications.
Mistake 4: Overlooking Fabrication and Welding Requirements
Another common mistake is failing to account for the fabrication and welding requirements of the stainless steel material. Different grades require specific welding techniques and filler materials to ensure a strong bond and maintain corrosion resistance.
Welding Considerations
- Filler Material Compatibility: Use filler materials that match the stainless steel grade to prevent weak joints and corrosion.
- Pre- and Post-Welding Treatments: Certain grades may require pre-heating or post-weld heat treatment to prevent cracking or corrosion.
Mistake 5: Not Evaluating Cost vs. Performance
While it’s tempting to select the least expensive stainless steel material, this approach can lead to long-term problems. Choosing a low-cost option without considering performance can result in higher maintenance costs, reduced durability, and even project failures.
Cost-Effectiveness Analysis
When evaluating cost, consider the following:
- Initial Cost vs. Lifecycle Cost: Assess the total cost of ownership, including maintenance and replacement costs over time.
- Quality vs. Price: Investing in higher-quality stainless steel may yield better performance and lower long-term costs.
Conclusion
Choosing the right stainless steel material is crucial for the success of any project. By avoiding these five common mistakes—overlooking the grade, underestimating surface finish importance, neglecting environmental factors, disregarding fabrication requirements, and failing to evaluate cost vs. performance—you can ensure your stainless steel selection enhances durability, efficiency, and overall project success.
Understanding the properties and applications of different stainless steel grades, as well as the significance of surface finishes and environmental considerations, will empower you to make informed decisions. Investing time in proper material selection will ultimately save you money and resources in the long run.
FAQ
Q1: What are the most common grades of stainless steel material?
A: The most common grades include 304 and 316 for austenitic stainless steel, 430 for ferritic stainless steel, and 410 for martensitic stainless steel.
Q2: How can I determine the best surface finish for my application?
A: Consider the environment, aesthetic requirements, and maintenance needs. Consult with suppliers or industry experts to find the most suitable finish.
Q3: Is it necessary to hire a professional for stainless steel welding?
A: Yes, hiring a qualified welder is essential, especially when working with specialized stainless steel grades, to ensure proper techniques and material compatibility.
Q4: Can I use stainless steel material in highly corrosive environments?
A: Yes, but it’s crucial to select a grade with high corrosion resistance, such as 316 stainless steel, to withstand harsh conditions effectively.
Q5: What factors should I consider when evaluating the cost of stainless steel material?
A: Assess both the initial cost and the total lifecycle cost, which includes maintenance, replacement, and overall performance over time.