Welcome to My Blog!
Before we dive into the content, I’d love for you to join me on my social media platforms where I share more insights, engage with the community, and post updates. Here’s how you can connect with me:
Facebook:https://www.facebook.com/profile.php?id=61559060896490
Now, let’s get started on our journey together. I hope you find the content here insightful, engaging, and valuable.
Introduction
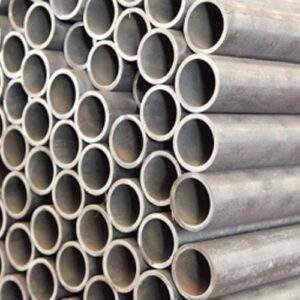
Precision steel tubes have revolutionized the manufacturing industry, offering a multitude of advantages over traditional steel pipes. Their superior accuracy, consistency, and mechanical properties make them indispensable in various applications, from automotive and aerospace to medical and mechanical engineering. In this comprehensive guide, we will delve into the numerous benefits of using precision steel tubes, exploring their key characteristics, applications, and factors to consider when selecting the right tube for your specific needs.
Understanding Precision Steel Tubes
What are Precision Steel Tubes? Precision steel tubes are highly accurate, seamless tubes manufactured to stringent tolerances. Unlike standard steel pipes, which often exhibit variations in wall thickness, diameter, and surface finish, precision tubes are characterized by their consistent dimensions and superior quality. This level of precision is achieved through advanced manufacturing techniques that ensure tight control over every stage of the production process.
Key Characteristics of Precision Steel Tubes
- High Dimensional Accuracy: Precision tubes are manufactured to precise tolerances, guaranteeing consistent dimensions and eliminating the need for secondary machining operations.
- Consistent Wall Thickness: Uniform wall thickness throughout the length of the tube ensures optimal strength and weight distribution.
- Smooth Inner and Outer Surfaces: Smooth surfaces minimize friction and improve fluid flow, making precision tubes ideal for hydraulic and pneumatic systems.
- Excellent Mechanical Properties: Precision tubes offer superior strength, durability, and resistance to fatigue, enabling them to withstand demanding operating conditions.
- Resistance to Corrosion: Many precision steel tubes are manufactured from corrosion-resistant alloys, making them suitable for applications exposed to harsh environments.
- Wide Range of Alloys and Grades: Precision tubes are available in a variety of alloys and grades, allowing manufacturers to select the optimal material for their specific requirements.
Advantages of Using Precision Steel Tubes in Manufacturing
- Enhanced Product Performance: Precision tubes contribute significantly to improved product performance by providing precise dimensions, strength, and durability. This results in products that are more reliable, efficient, and long-lasting.
- Reduced Manufacturing Costs: The use of precision steel tubes can lead to significant cost savings throughout the manufacturing process. By eliminating the need for additional machining and finishing operations, manufacturers can reduce labor costs, material waste, and energy consumption.
- Improved Efficiency: Precision tubes streamline manufacturing processes by simplifying assembly and reducing the risk of errors. This leads to increased productivity and faster time-to-market.
- Increased Product Life: The superior quality and durability of precision tubes extend the lifespan of products, reducing the need for frequent repairs and replacements. This translates into lower maintenance costs and increased customer satisfaction.
Applications of Precision Steel Tubes
Precision steel tubes have a wide range of applications across various industries, including:
- Automotive Industry: Precision tubes are used in a variety of automotive components, such as suspension systems, brake lines, fuel lines, and exhaust systems. Their high strength-to-weight ratio and resistance to corrosion make them ideal for demanding automotive applications.
- Aerospace Industry: The aerospace industry relies on precision tubes for critical components, including landing gear, hydraulic systems, and engine components. The stringent requirements for weight reduction, strength, and reliability in aerospace applications are met by the exceptional properties of precision tubes.
- Mechanical Engineering: Precision tubes find applications in various mechanical engineering components, such as bearings, shafts, and hydraulic cylinders. Their precise dimensions and superior mechanical properties ensure optimal performance and efficiency.
- Medical Equipment: The medical industry utilizes precision tubes in the manufacturing of surgical instruments, medical implants, and diagnostic equipment. The high level of precision and cleanliness required in medical applications is met by the stringent quality standards of precision steel tubes.
Comparison of Precision Steel Tubes and Standard Steel Pipes
Feature | Precision Steel Tubes | Standard Steel Pipes |
---|---|---|
Dimensional Accuracy | High | Low |
Wall Thickness | Consistent | Variable |
Surface Finish | Smooth | Rough |
Mechanical Properties | Superior | Standard |
Cost | Higher | Lower |
Factors to Consider When Selecting Precision Steel Tubes
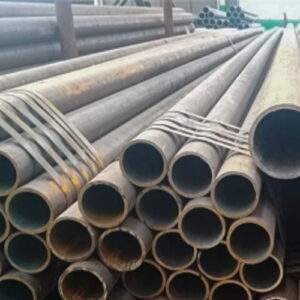
When selecting precision steel tubes for a specific application, several factors should be considered:
- Material Grade: The choice of material grade depends on the specific requirements of the application, such as corrosion resistance, strength, and temperature tolerance. Common alloy options include stainless steel, carbon steel, and alloy steel.
- Dimensions: Precision tubes are available in a wide range of sizes and dimensions, including outer diameter, wall thickness, and length. It is essential to select the appropriate dimensions to ensure proper fit and function.
- Tolerances: The required tolerances determine the manufacturing process and the level of precision required. Tight tolerances are essential for applications demanding high accuracy and performance.
- Surface Finish: The desired surface finish affects the performance and appearance of the final product. Smooth surface finishes are ideal for applications requiring low friction and improved fluid flow.
Conclusion
Precision steel tubes have emerged as a critical component in modern manufacturing, offering numerous advantages over traditional steel pipes. Their superior accuracy, consistency, and mechanical properties make them the preferred choice for engineers and manufacturers seeking to optimize their products and processes. By understanding the benefits and applications of precision tubes, manufacturers can enhance product performance, reduce costs, and improve overall efficiency.
FAQ
What is the difference between precision steel tubes and standard steel pipes?
Precision steel tubes are manufactured to much tighter tolerances than standard steel pipes, resulting in superior accuracy, consistency, and surface finish.
How are precision tubes manufactured?
Precision tubes are typically manufactured through seamless processes such as cold drawing or hot rolling, followed by precision machining to achieve the desired dimensions and tolerances.
What are the common alloys used for precision steel tubes?
Common alloys used for precision steel tubes include stainless steel, carbon steel, and alloy steel. The choice of alloy depends on the specific application requirements, such as corrosion resistance, strength, and temperature tolerance.
How do I choose the right precision steel tube for my application?
To select the right precision steel tube for your application, consider factors such as material grade, dimensions, tolerances, surface finish, and mechanical properties. Consulting with a knowledgeable supplier or engineer can help you make the best choice.