Welcome to My Blog!
Before we dive into the content, I’d love for you to join me on my social media platforms where I share more insights, engage with the community, and post updates. Here’s how you can connect with me:
Facebook:https://www.facebook.com/profile.php?id=61559060896490
Now, let’s get started on our journey together. I hope you find the content here insightful, engaging, and valuable.
Table of Contents
Introduction
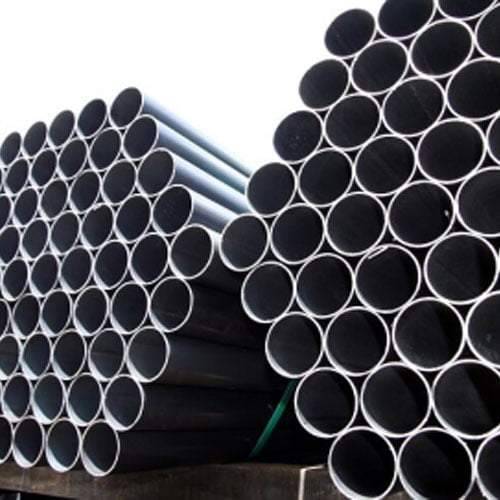
Selecting the appropriate boiler tube material is a critical decision that significantly impacts the performance, efficiency, and longevity of a boiler system. Boiler tubes are subjected to extreme conditions, including high temperatures and pressures, which can lead to wear and tear over time. Therefore, understanding the characteristics of different boiler tube materials is essential for ensuring the reliability and efficiency of your boiler operations.
This blog will delve into the various types of boiler tube materials, their properties, advantages, disadvantages, and how to choose the right material for your specific application. Additionally, we will discuss best practices for maintaining boiler tubes to extend their lifespan. By the end of this article, you will have a comprehensive understanding of boiler tube material selection and how it affects boiler performance.
Understanding Boiler Tube Materials
Boiler tubes are made from various materials, each offering unique properties that make them suitable for specific applications. The primary materials used for boiler tubes include:
- Carbon Steel
- Alloy Steel
- Stainless Steel
- Copper-Nickel Alloys
- Specialty Alloys
Each type of material has its advantages and drawbacks, and the selection process must consider factors such as operating conditions, cost, and maintenance requirements.
Types of Boiler Tube Materials
Carbon Steel
Overview: Carbon steel is the most commonly used material for boiler tubes due to its excellent strength-to-weight ratio and cost-effectiveness. It can withstand high pressures and temperatures, making it suitable for many industrial applications.
Advantages:
- Economical and readily available.
- High tensile strength.
- Good weldability.
Disadvantages:
- Susceptible to corrosion in certain environments.
- Limited resistance to high temperatures compared to alloy steels.
Common Applications:
- Fire-tube boilers.
- Lower pressure water-tube boilers.
Alloy Steel
Overview: Alloy steel is designed to improve certain properties such as strength, hardness, and corrosion resistance. It contains elements like chromium, molybdenum, and nickel, which enhance its performance in high-temperature applications.
Advantages:
- Higher temperature and pressure resistance than carbon steel.
- Improved toughness and ductility.
- Enhanced corrosion resistance.
Disadvantages:
- More expensive than carbon steel.
- Requires more careful handling during welding.
Common Applications:
- High-pressure steam boilers.
- Power generation plants.
Stainless Steel
Overview: Stainless steel is known for its excellent corrosion resistance and durability. It contains chromium, which forms a protective oxide layer on the surface, making it suitable for harsh environments.
Advantages:
- Outstanding corrosion resistance.
- High-temperature tolerance.
- Low maintenance requirements.
Disadvantages:
- Higher cost compared to carbon and alloy steels.
- Can be more difficult to weld.
Common Applications:
- Waste heat recovery systems.
- Boilers in chemical processing.
Copper-Nickel Alloys
Overview: Copper-nickel alloys are used in applications where seawater or other corrosive media are present. Their resistance to corrosion makes them ideal for marine and chemical applications.
Advantages:
- Excellent corrosion resistance, especially in marine environments.
- Good thermal conductivity.
- Low thermal expansion.
Disadvantages:
- Higher cost.
- Limited mechanical strength compared to steel.
Common Applications:
- Marine boilers.
- Desalination plants.
Specialty Alloys
Overview: Specialty alloys, such as Inconel and Monel, are engineered for extreme conditions, including high temperatures and corrosive environments. They are often used in specialized applications where standard materials are insufficient.
Advantages:
- Exceptional resistance to high temperatures and corrosion.
- Retain strength in extreme conditions.
Disadvantages:
- Very high cost.
- Limited availability.
Common Applications:
- Aerospace applications.
- Advanced power generation systems.
Comparison of Boiler Tube Materials
Understanding the differences between various boiler tube materials can aid in selecting the most suitable option for your specific application. The table below summarizes the key characteristics of the common boiler tube materials:
Material Type | Temperature Resistance | Pressure Resistance | Corrosion Resistance | Cost | Common Applications |
---|---|---|---|---|---|
Carbon Steel | Moderate | High | Low | Low | Fire-tube boilers, lower pressure systems |
Alloy Steel | High | Very High | Moderate | Moderate | High-pressure steam boilers, power plants |
Stainless Steel | Very High | Moderate | High | High | Chemical processing, waste heat recovery |
Copper-Nickel Alloys | High | Moderate | Very High | High | Marine applications, desalination plants |
Specialty Alloys | Extremely High | Very High | Very High | Very High | Aerospace, advanced power generation |
This comparison table provides an overview of the key attributes of each boiler tube material, aiding you in making an informed decision based on your specific needs.
Factors to Consider When Selecting Boiler Tube Material
Choosing the right boiler tube material involves several critical considerations. Here are some factors to take into account:
Operating Conditions
Understanding the operating temperature and pressure of your boiler is essential. For high-temperature and high-pressure applications, alloy or specialty steels may be more appropriate, whereas carbon steel may suffice for lower demands.
Corrosion Resistance
If your boiler operates in a corrosive environment, consider materials with high corrosion resistance, such as stainless steel or copper-nickel alloys. Assess the types of fluids and gases that will be present in the system.
Cost and Budget
Cost is a significant factor in material selection. While higher-grade materials may offer better performance and longevity, they can also increase initial investment costs. Balance your budget with performance needs.
Maintenance Requirements
Different materials have varying maintenance needs. Stainless steel, for instance, may require less maintenance than carbon steel. Assess the maintenance resources available and choose a material that aligns with your capabilities.
Weldability
If your boiler design involves extensive welding, consider the weldability of the material. Some materials, like carbon steel, are easier to weld than others, such as stainless steel or specialty alloys.
Best Practices for Boiler Tube Maintenance
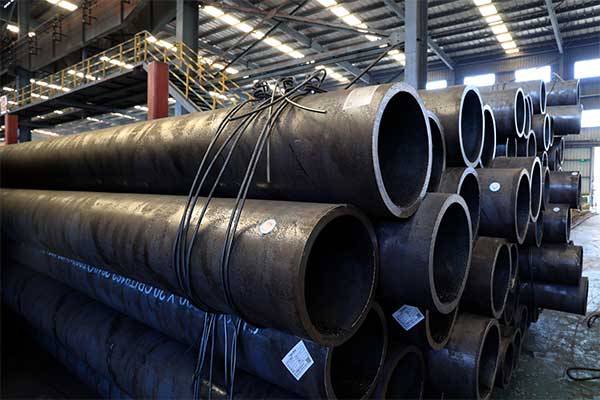
Proper maintenance of boiler tubes is essential to ensure their longevity and efficiency. Here are some best practices for maintaining boiler tubes:
Regular Inspections
Conduct regular inspections to identify any signs of wear, corrosion, or damage. Early detection can help prevent major issues and extend the life of the tubes.
Proper Cleaning
Boiler tubes should be cleaned regularly to remove soot, scale, and other deposits. Neglecting this step can reduce heat transfer efficiency and increase fuel consumption.
Monitoring Operating Conditions
Monitor the operating conditions of the boiler closely. Ensure that the temperature and pressure remain within the recommended limits to avoid overstressing the tubes.
Use of Corrosion Inhibitors
In corrosive environments, consider using corrosion inhibitors to protect boiler tubes from chemical damage. These compounds can significantly extend the lifespan of the tubes.
Timely Repairs and Replacements
If any signs of damage or wear are detected, address them immediately by repairing or replacing the affected tubes. Timely action can prevent more significant problems down the line.
Conclusion
The selection of boiler tube material is a vital aspect of ensuring the efficiency, safety, and longevity of your boiler system. By understanding the various types of boiler tube materials and their respective advantages and disadvantages, you can make informed decisions that best suit your operational needs.
Incorporating best practices for maintenance will further enhance the performance of your boiler tubes, minimizing downtime and maximizing productivity. Whether you choose carbon steel, alloy steel, stainless steel, or specialty alloys, remember that the right material can make all the difference in the success of your boiler operations.
FAQ
What is the best material for boiler tubes?
The best material for boiler tubes depends on the specific application and operating conditions. Alloy steel is often preferred for high-pressure applications, while carbon steel is suitable for lower pressures.
How often should boiler tubes be inspected?
Boiler tubes should be inspected at least once a year, but more frequent inspections may be required in high-pressure or high-temperature systems.
Can I use carbon steel tubes in high-temperature applications?
While carbon steel tubes can handle moderate temperatures, they may not be suitable for high-temperature applications. Alloy or specialty steels are better choices for such conditions.
What are the signs of boiler tube failure?
Signs of boiler tube failure include leaks, reduced efficiency, unusual noises, and visible corrosion or scaling. Regular inspections can help identify these issues early.
How can I improve the lifespan of boiler tubes?
To improve the lifespan of boiler tubes, conduct regular inspections, clean them frequently, monitor operating conditions, use corrosion inhibitors, and address repairs promptly.