Welcome to My Blog!
Before we dive into the content, I’d love for you to join me on my social media platforms where I share more insights, engage with the community, and post updates. Here’s how you can connect with me:
Facebook:https://www.facebook.com/profile.php?id=61559060896490
Now, let’s get started on our journey together. I hope you find the content here insightful, engaging, and valuable.
Introduction
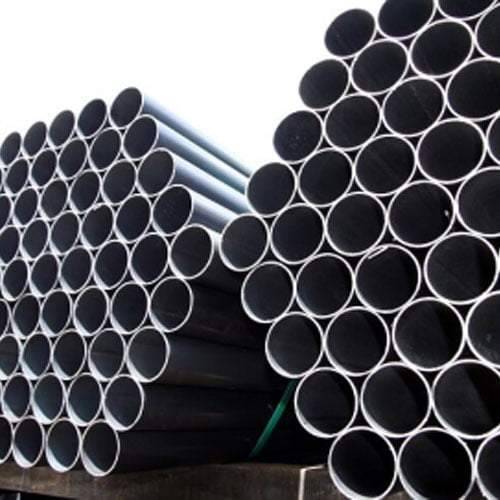
The choice of boiler water tube material is crucial in ensuring the longevity and efficiency of industrial boilers. Boilers play an essential role in various industries, including power generation, manufacturing, and heating, and must operate under challenging conditions. The water tubes are subjected to extreme temperatures, high pressures, and corrosive environments, which can significantly impact their performance and lifespan. Choosing the right material is vital not only for maintaining efficiency but also for ensuring safety in boiler operations. In this blog, we will delve into the various factors affecting the durability of boiler water tube materials. By understanding these factors, engineers and facility managers can make informed decisions that enhance the reliability of their boiler systems.
Importance of Choosing the Right Boiler Water Tube Material
Selecting the appropriate boiler water tube material is vital for several reasons. First and foremost, the material affects the operational efficiency of the boiler system. For instance, materials with excellent thermal conductivity can enhance heat transfer rates, leading to more efficient energy use. Additionally, the right material can improve safety standards, as inadequate materials can fail under pressure, resulting in leaks, explosions, or other dangerous situations. Durability and resistance to wear and tear are critical; durable materials reduce the likelihood of failure, which can lead to costly downtimes and repairs. Furthermore, while high-quality materials may come with a higher initial investment, they often lead to significant long-term savings. This is due to reduced maintenance needs, lower operational costs, and extended service life. Understanding the implications of material selection can help stakeholders make informed decisions that will ultimately enhance boiler performance and safety.
Factors Affecting Durability of Boiler Water Tube Material
Temperature and Pressure Conditions
Boiler systems operate under high temperatures and pressures, which can cause significant stress on the water tubes. The selected material must be able to withstand these extreme conditions without deforming or failing. For example, common materials used include carbon steel, alloy steel, and stainless steel, each with its unique characteristics regarding heat tolerance and strength. Carbon steel is generally cost-effective but may not perform well at very high temperatures or pressures. On the other hand, alloy steels offer improved strength and temperature resistance, making them more suitable for high-performance applications. Understanding the specific operational parameters of the boiler is essential for selecting the right material, as each material will have a defined threshold for temperature and pressure beyond which it may fail.
Corrosion Resistance
Corrosion is a significant factor that can compromise the integrity of boiler water tube materials. The presence of water, steam, and various chemicals can lead to rust and corrosion over time. The types of fuels used can also contribute to corrosive environments; for instance, burning coal can produce acidic flue gases that accelerate corrosion. Materials that are resistant to corrosion, such as stainless steel and specially alloyed steels, tend to have a longer lifespan and require less frequent replacement. Moreover, protective coatings and surface treatments can also enhance corrosion resistance, extending the life of the water tubes. Regular monitoring of the internal and external conditions of the boiler system is crucial in identifying potential corrosion issues before they lead to significant damage.
Mechanical Properties
The mechanical properties of boiler water tube materials, such as tensile strength, yield strength, and hardness, are crucial for durability. Tensile strength refers to the maximum amount of tensile (pulling) stress a material can withstand before failure. Similarly, yield strength is the amount of stress at which a material begins to deform plastically. Materials with higher mechanical strength can better withstand the operational stresses without deforming or failing. It is essential to select materials that not only meet the operational demands but also comply with industry standards. Testing mechanical properties during the material selection process can ensure that the chosen materials will perform effectively under the expected operational conditions.
Fabrication and Weldability
The ability to fabricate and weld boiler water tube materials effectively is also a key consideration. Some materials can be challenging to work with, leading to potential weaknesses in weld joints. For example, certain high-strength alloys may be difficult to weld without causing stress concentrations or defects in the weld area. This can compromise the overall integrity of the boiler structure. Materials that are easier to weld and form can help ensure the structural integrity of the boiler during operation. Proper welding techniques, including preheating and post-weld heat treatment, can enhance the performance of welded joints. Therefore, understanding the fabrication characteristics of each material is essential for ensuring reliable and durable boiler water tubes.
Operating Environment
The specific operating environment can also impact the choice of boiler water tube material. Factors such as the presence of flue gases, the type of fuel used, and the overall system design can influence material selection. For instance, if a boiler operates in a highly corrosive environment, choosing a material with high corrosion resistance is paramount. Additionally, the presence of mechanical stressors such as vibration or thermal cycling can also affect material performance. Understanding these environmental factors helps in choosing a material that will endure the specific challenges presented by the boiler’s operation. This tailored approach to material selection ensures that the boiler system remains efficient and reliable over its operational lifetime.
Comparison of Common Boiler Water Tube Materials
Different materials are utilized for boiler water tubes, each offering distinct benefits and drawbacks. The following table summarizes the properties of various boiler water tube materials, helping stakeholders make informed choices.
Table: Properties of Various Boiler Water Tube Materials
Material | Corrosion Resistance | Max Temperature (°C) | Max Pressure (bar) | Weldability | Cost |
---|---|---|---|---|---|
Carbon Steel | Moderate | 400 | 40 | Good | Low |
Alloy Steel | High | 540 | 60 | Moderate | Medium |
Stainless Steel | Very High | 700 | 100 | Good | High |
Copper-Nickel Alloy | High | 300 | 50 | Moderate | High |
Titanium Alloys | Excellent | 800 | 100 | Poor | Very High |
In the table above, we can see that carbon steel is the most economical option, but its limitations in high-temperature and high-pressure applications make it less suitable for advanced boiler systems. Alloy steels provide a balance between performance and cost, offering enhanced durability without the high price tag of stainless steel. Stainless steel is often favored in corrosive environments due to its superior resistance to rust and degradation. Copper-nickel alloys are also used for their excellent corrosion resistance, especially in marine applications, but their cost can be prohibitive. Lastly, titanium alloys, while offering the best performance, are generally reserved for specialized applications due to their high cost and difficult weldability.
Maintenance and Inspection Practices
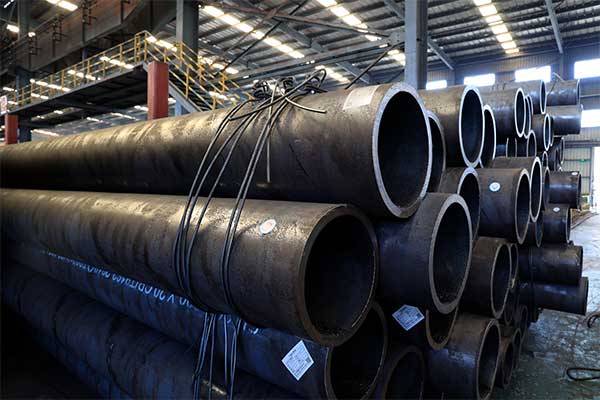
Proper maintenance and regular inspection of boiler water tube materials are essential for ensuring their longevity. Here are some best practices to follow:
- Regular Cleaning: Deposits and scaling can reduce efficiency and cause corrosion. Implementing a cleaning schedule to remove buildup can significantly enhance performance. Various cleaning methods, such as chemical cleaning and mechanical cleaning, can be employed depending on the severity of the buildup.
- Periodic Inspections: Conduct regular inspections to identify signs of wear, corrosion, or fatigue. Non-destructive testing methods, such as ultrasonic testing, radiography, or magnetic particle testing, can help detect flaws without damaging the boiler components. These inspections should be conducted based on a predetermined schedule or triggered by specific operational conditions.
- Monitoring Operating Conditions: Keeping an eye on the operating temperature, pressure, and chemical composition of the water can help prevent conditions that may lead to premature failure. Automated monitoring systems can provide real-time data, enabling prompt responses to any anomalies in operation.
- Implementing a Maintenance Program: Establishing a comprehensive maintenance program that includes scheduled maintenance, inspections, and performance evaluations can enhance the reliability and longevity of the boiler system.
By adhering to these maintenance practices, facility managers can significantly extend the lifespan of boiler water tubes and reduce the risk of unexpected failures.
Conclusion
Choosing the right boiler water tube material is vital for ensuring the durability and efficiency of boiler systems. Factors such as temperature and pressure conditions, corrosion resistance, mechanical properties, fabrication, and operating environment all play a crucial role in determining the longevity of these materials. By understanding these factors and selecting the appropriate materials, engineers and facility managers can optimize boiler performance, reduce maintenance costs, and enhance safety in their operations. Regular maintenance and inspection practices further contribute to the longevity of boiler water tube materials, ensuring they remain reliable under demanding conditions. Ultimately, the right choice in boiler water tube material not only ensures safety and efficiency but also leads to substantial savings and increased productivity in industrial applications.
FAQ
What materials are commonly used for boiler water tubes?
Common materials for boiler water tubes include carbon steel, alloy steel, stainless steel, copper-nickel alloys, and titanium alloys, each chosen based on specific operational requirements. The selection is often influenced by the operating environment, pressure, temperature, and resistance to corrosion.
How does temperature affect boiler water tube material?
Higher temperatures can lead to material degradation, so it’s essential to select materials that can withstand the maximum operating temperature of the boiler without losing strength. Operating at temperatures exceeding the material’s threshold can result in deformation, reduced efficiency, and increased risk of failure.
What role does corrosion play in boiler water tube durability?
Corrosion is a primary factor that can reduce the lifespan of boiler water tubes. The combination of high temperatures, moisture, and certain chemicals can accelerate the corrosion process. Materials with high corrosion resistance can help mitigate this issue and enhance durability, prolonging the life of the water tubes.
How often should boiler water tubes be inspected?
Boiler water tubes should be inspected regularly, typically on an annual basis or more frequently if operating conditions are harsh or if there are signs of wear. Establishing a routine inspection schedule ensures that any potential issues are identified and addressed promptly.
What is the importance of weldability in boiler water tube materials?
Weldability is crucial because poor weld joints can become weak points in the structure, potentially leading to failure. Materials that are easier to weld contribute to overall durability. Proper welding techniques and practices can help ensure strong joints that maintain the integrity of the boiler system.