Welcome to My Blog!
Before we dive into the content, I’d love for you to join me on my social media platforms where I share more insights, engage with the community, and post updates. Here’s how you can connect with me:
Facebook:https://www.facebook.com/profile.php?id=61559060896490
Now, let’s get started on our journey together. I hope you find the content here insightful, engaging, and valuable.
Introduction
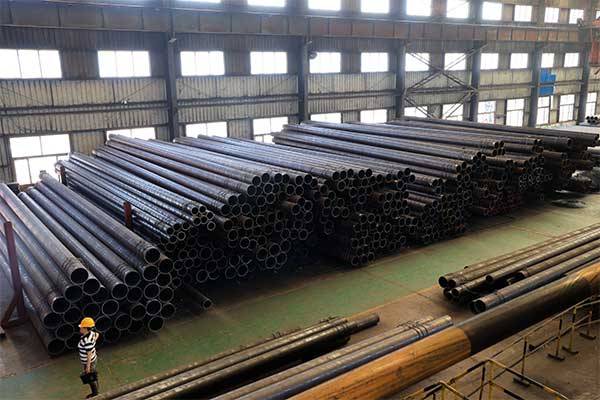
Selecting the appropriate mechanical tube size is a critical decision in various engineering applications. Whether you’re working on a construction project, manufacturing a product, or designing a custom machine, the correct mechanical tube size directly impacts the overall performance, durability, and cost-effectiveness of your system. In this comprehensive guide, we’ll delve into the factors influencing mechanical tube size selection and provide practical tips to help you make informed choices.
Understanding Mechanical Tube Sizes
Mechanical tubes come in a wide range of sizes, specified by their outer diameter and wall thickness. These dimensions are crucial for determining a tube’s strength, capacity, and suitability for a particular application.
Outer Diameter: The outer diameter of a mechanical tube affects its overall strength and the amount of fluid or material it can carry. A larger outer diameter generally provides greater strength and capacity, but it also increases the overall size and weight of the tube.
Wall Thickness: The wall thickness determines a mechanical tube’s resistance to pressure, corrosion, and wear. Thicker walls provide greater strength and durability, but they also increase the weight and cost of the tube. The choice of wall thickness depends on the specific application and the required pressure rating.
Factors Influencing Mechanical Tube Size Selection
Several factors must be considered when choosing the right mechanical tube size, including:
- Application: The specific use of the mechanical tube will dictate the required size. For instance, tubes used for structural support will have different requirements than those used for fluid conveyance. Structural tubes may require larger outer diameters and thicker walls to ensure sufficient strength, while tubes used for fluid conveyance may prioritize flow capacity and pressure resistance.
- Material: The material of the mechanical tube, such as stainless steel, aluminum, or copper, will affect its strength, weight, and corrosion resistance. Stainless steel is often used in applications where corrosion resistance is a primary concern, while aluminum is a lightweight option suitable for many applications. Copper is known for its excellent thermal and electrical conductivity and is commonly used in heat exchangers and electrical wiring.
- Pressure: The maximum operating pressure that the mechanical tube will experience is a critical factor in determining the required wall thickness. Higher pressure ratings require thicker walls to prevent the tube from bursting or deforming. The material of the mechanical tube also plays a role in its pressure resistance.
- Temperature: The operating temperature range will influence the choice of material and wall thickness. Some materials, such as high-temperature alloys, are specifically designed to withstand extreme temperatures. Additionally, the thermal expansion and contraction of the mechanical tube must be considered to prevent stress-related failures.
- Corrosion: If the mechanical tube will be exposed to corrosive environments, a corrosion-resistant material and appropriate wall thickness are necessary. The choice of material depends on the specific corrosive agents involved. For example, stainless steel is highly resistant to many acids and alkalis, while copper is susceptible to corrosion in certain environments.
- Cost: The cost of the mechanical tube and associated fittings is an important consideration, but it should not compromise performance or safety. Factors such as material cost, manufacturing processes, and tube size can influence the overall cost. It is important to balance cost with the long-term benefits of selecting the appropriate mechanical tube size.
Common Applications for Mechanical Tubes
Mechanical tubes are used in a wide range of applications, including:
- Construction: Structural support, piping systems, and railings.
- Manufacturing: Conveying fluids, gases, and solids; producing components.
- Automotive: Fuel lines, brake lines, and chassis components.
- Aerospace: Hydraulic systems and structural components.
- Energy: Piping systems for oil, gas, and water; heat exchangers.
- Medical: Medical equipment and devices.
- Marine: Piping systems and structural components.
Selecting the Right Mechanical Tube Size: A Step-by-Step Guide
- Define the application: Clearly outline the specific purpose of the mechanical tube. Consider factors such as the type of fluid or material it will carry, the operating pressure and temperature, and any environmental conditions it will be exposed to.
- Determine the required material: Consider factors such as strength, corrosion resistance, cost, and availability. Research the properties of different materials and select the one that best meets the requirements of your application.
- Calculate the required dimensions: Use engineering formulas and standards to determine the necessary outer diameter and wall thickness for the mechanical tube. Consider factors such as the flow rate, pressure, and temperature to ensure that the tube can handle the intended load.
- Consider manufacturing tolerances: Account for variations in mechanical tube dimensions during the manufacturing process. Allow for a certain degree of tolerance to ensure proper fit and function.
- Select appropriate fittings: Ensure that the fittings are compatible with the mechanical tube size and material. Consider factors such as the type of connection (threaded, welded, or flanged), the pressure rating, and the compatibility with the tube material.
Tube Size Comparison Table
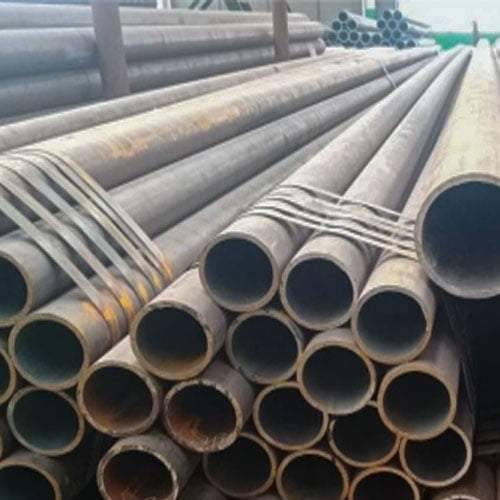
Application | Material | Outer Diameter | Wall Thickness | Pressure Rating |
---|---|---|---|---|
Hydraulic system | Stainless steel | 1/2 inch | 0.065 inch | 3000 psi |
Natural gas line | Carbon steel | 3/4 inch | 0.109 inch | 150 psi |
Structural support | Aluminum | 2 inches | 0.125 inch | N/A |
Conclusion
Choosing the correct mechanical tube size is essential for ensuring the safety, reliability, and efficiency of your system. By carefully considering the factors discussed in this guide, you can make informed decisions and select the most suitable mechanical tubes for your project.
FAQ
What is the difference between a pipe and a tube?
A pipe is typically larger and has thicker walls than a tube. Tubes are often used for conveying fluids or materials, while pipes are more commonly used for structural support or large-scale fluid transport.
How do I calculate the wall thickness of a mechanical tube?
The wall thickness of a mechanical tube can be calculated using engineering formulas that take into account the required pressure, material properties, and other factors.
What are the standard units for measuring mechanical tube sizes?
Mechanical tube sizes are typically measured in inches or millimeters.
What are the common materials used for mechanical tubes?
Common materials for mechanical tubes include stainless steel, aluminum, copper, carbon steel, and high-temperature alloys.