Welcome to My Blog!
Before we dive into the content, I’d love for you to join me on my social media platforms where I share more insights, engage with the community, and post updates. Here’s how you can connect with me:
Facebook:https://www.facebook.com/profile.php?id=61559060896490
Now, let’s get started on our journey together. I hope you find the content here insightful, engaging, and valuable.
Table of Contents
Introduction
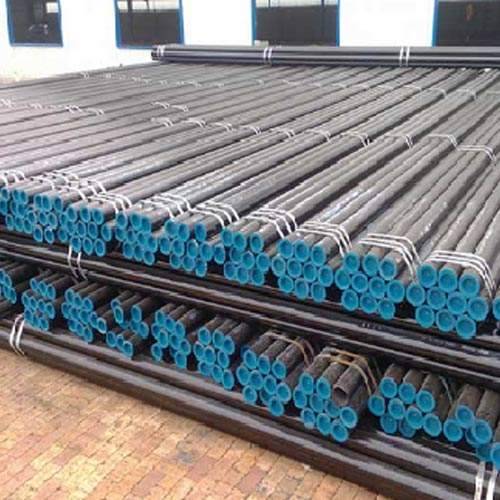
Cold drawn precision seamless steel tubes are the epitome of precision engineering, offering exceptional quality and performance. These tubes are produced through a meticulous process involving cold working, which significantly enhances their mechanical properties and dimensional accuracy. The absence of welds ensures superior strength and resistance to pressure, making them ideal for demanding applications across various industries.
Why Choose Cold Drawn Precision Seamless Steel Tubes?
- Unmatched Precision: The cold drawing process results in extremely tight tolerances, making these tubes perfect for applications requiring precise dimensions and tolerances.
- Superior Strength and Durability: Cold working significantly increases the tensile strength, yield strength, and hardness of the tubes, ensuring long-lasting performance.
- Smooth Surface Finish: The cold drawing process produces a smooth and bright surface finish, reducing the need for additional finishing processes and improving the overall appearance.
- Versatility and Customization: Available in a wide range of sizes, grades, and alloys, cold drawn precision seamless steel tubes can be tailored to meet specific application requirements.
The Cold Drawing Process: A Step-by-Step Breakdown
The cold drawing process is a complex yet efficient method that involves several key steps:
- Heating: The steel billet is heated to a specific temperature to enhance its ductility and make it more pliable for the subsequent drawing process.
- Piercing: The heated billet is pierced to create a hollow tube, forming the initial shape of the future product.
- Reducing: The pierced tube is drawn through a series of dies, each with a progressively smaller diameter. This drawing process reduces the tube’s diameter and elongates its length, simultaneously increasing its strength and precision.
- Annealing: After each drawing pass, the tube may undergo annealing to relieve internal stresses and maintain its ductility. This step is crucial for ensuring the tube’s structural integrity and preventing potential defects.
- Straightening: The final step involves straightening the tube to achieve the desired straightness and dimensional accuracy. This process ensures that the tube meets the stringent quality standards required for various applications.
Applications of Cold Drawn Precision Seamless Steel Tubes: A Diverse Range
Cold drawn precision seamless steel tubes find applications in a multitude of industries, where their superior properties and precision are essential:
- Automotive Industry: Axles, steering columns, hydraulic cylinders, and other critical components benefit from the strength and durability of cold drawn tubes.
- Aerospace Industry: Landing gear, hydraulic lines, structural components, and other aerospace components require the high-performance characteristics of cold drawn tubes.
- Mechanical Engineering: Bearings, shafts, spindles, and other precision components rely on the accuracy and reliability of cold drawn tubes.
- Oil and Gas Industry: Tubing, drill pipes, fittings, and other components used in the demanding oil and gas industry benefit from the strength and corrosion resistance of cold drawn tubes.
- Medical Industry: Surgical instruments, implants, and other medical devices require the precision and biocompatibility of cold drawn tubes.
Materials Used for Cold Drawn Precision Seamless Steel Tubes: Tailored for Specific Needs
Cold drawn tubes can be produced from a variety of steel grades, each offering unique properties to suit specific applications:
- Carbon Steel: Offers a good balance of strength, ductility, and cost-effectiveness, making it suitable for a wide range of general-purpose applications.
- Alloy Steel: Provides enhanced properties such as increased strength, improved corrosion resistance, and higher temperature resistance, making it ideal for demanding environments and critical applications.
- Stainless Steel: Offers exceptional corrosion resistance, high temperature strength, and excellent hygiene properties, making it suitable for applications in the food, pharmaceutical, and chemical industries.
Tolerances and Standards: Ensuring Quality and Consistency
Cold drawn precision seamless steel tubes are manufactured to stringent tolerances to ensure dimensional accuracy and consistency. Common standards governing the production of these tubes include:
- ASTM A519: Specification for Seamless Carbon and Alloy Steel Mechanical Tubing
- ASTM A213: Specification for Seamless Ferritic and Austenitic Alloy Steel Boiler and Superheater Tubes
Comparison of Cold Drawn and Hot Rolled Seamless Tubes
Feature | Cold Drawn Seamless | Hot Rolled Seamless |
---|---|---|
Dimensional Accuracy | Extremely High | Moderate |
Surface Finish | Smooth and Bright | Rougher |
Mechanical Properties | Superior Strength, Hardness, and Ductility | Lower Strength and Ductility |
Cost | Higher | Lower |
Quality Control and Testing: Rigorous Standards for Excellence
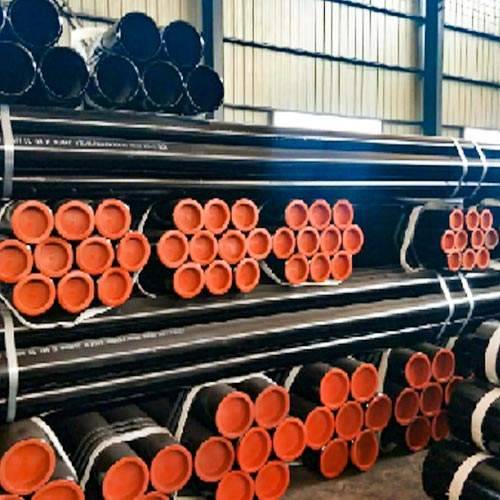
To ensure the highest quality standards, manufacturers of cold drawn precision seamless steel tubes implement rigorous quality control measures and conduct various tests:
- Dimensional Inspection: To verify that the tubes meet the specified tolerances and dimensions.
- Mechanical Testing: To determine tensile strength, yield strength, elongation, and other mechanical properties.
- Non-destructive Testing: To detect any defects such as cracks, inclusions, or porosity, ensuring the structural integrity of the tubes.
Conclusion
Cold drawn precision seamless steel tubes represent the pinnacle of precision engineering, offering exceptional quality, performance, and reliability. Their diverse applications, coupled with their superior properties, make them indispensable components in various industries. As technology continues to advance, we can expect further innovations in the production and application of these remarkable tubes, shaping the future of precision engineering.
FAQ
What is the difference between cold drawn and hot rolled seamless tubes?
Cold drawn tubes offer superior precision, a smoother surface finish, and significantly enhanced mechanical properties compared to hot rolled tubes.
What are the common applications of cold drawn precision seamless steel tubes?
Cold drawn tubes find applications in a wide range of industries, including automotive, aerospace, mechanical engineering, oil and gas, and medical.
What materials are used for cold drawn precision seamless steel tubes?
Cold drawn tubes can be produced from various steel grades, including carbon steel, alloy steel, and stainless steel.