Welcome to My Blog!
Before we dive into the content, I’d love for you to join me on my social media platforms where I share more insights, engage with the community, and post updates. Here’s how you can connect with me:
Facebook:https://www.facebook.com/profile.php?id=61559060896490
Now, let’s get started on our journey together. I hope you find the content here insightful, engaging, and valuable.
Introduction
Boiler tubes play a vital role in transferring heat and maintaining the stability of the entire boiler system. With different applications requiring specific tube types, understanding the various options and their unique properties is key to selecting the best match for your operations. In this guide, we explore all essential aspects of boiler tubes to ensure you’re equipped with the knowledge to make an informed decision.
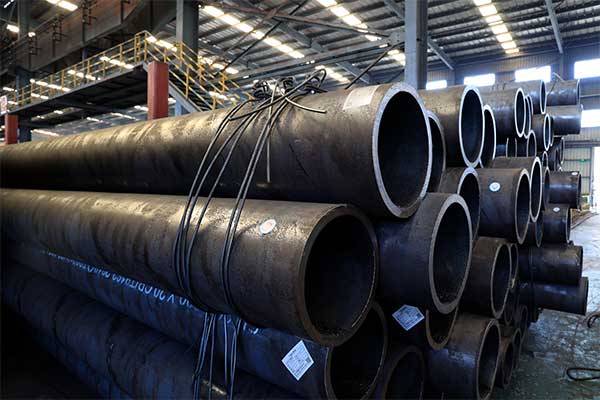
Understanding Boiler Tube Basics
Boiler tubes are specially designed tubes used to carry water, steam, or gases at high pressure and temperature within boiler systems. These tubes must withstand high temperatures, corrosion, and pressure, making the selection process critical to system longevity.
Basic Properties of Boiler Tubes | Explanation |
---|---|
High Heat Resistance | Must endure high operational temperatures |
Corrosion Resistance | Essential for longevity and maintenance |
Mechanical Strength | Must resist pressure without deformation |
Thermal Conductivity | Ensures efficient heat transfer |
The design of boiler tubes varies to suit specific applications, so selecting the right type directly impacts the boiler’s performance and maintenance schedule.
Key Material Considerations
Choosing the right material for your boiler tubes is foundational to ensuring durability and efficiency. Here are some commonly used materials and their characteristics:
- Carbon Steel: Affordable, high strength, suitable for moderate temperatures.
- Stainless Steel: Corrosion-resistant, ideal for high-temperature applications.
- Alloy Steel: Tailored to withstand extreme temperatures and pressures.
- Copper-Nickel Alloys: Known for corrosion resistance, ideal for marine environments.
Understanding the properties of each material helps determine which is best suited for specific conditions, like high-temperature resistance or low corrosive environments.
Types of Boiler Tubes
Boiler tubes can be classified into various types based on their applications. Common categories include:
Fire-Tube Boiler Tubes
Used primarily in low- to moderate-pressure applications, fire-tube boiler tubes allow hot gases to flow through the tubes, with water surrounding them to be heated.
Water-Tube Boiler Tubes
Water-tube boiler tubes operate at higher pressures and are ideal for industrial applications. In this setup, water flows through the tubes surrounded by hot gases, making it suitable for applications requiring rapid heating.
Heat Recovery Steam Generator (HRSG) Tubes
Used in combined cycle power plants, HRSG tubes recover heat from gas turbine exhaust to generate steam, increasing efficiency.
Each of these types serves different applications, and selecting the right one can depend heavily on the operational requirements of your boiler.
Size and Thickness Specifications
The size and thickness of boiler tubes play a critical role in determining their strength and efficiency. Factors to consider include:
- Outer Diameter (OD): Impacts the tube’s strength and heat exchange capabilities.
- Wall Thickness: Directly influences pressure resistance and durability.
Tube Specification | Recommended Application |
---|---|
OD: 1-5 inches | Low- to moderate-pressure systems |
OD: 6-10 inches | High-pressure industrial applications |
Wall Thickness: 0.5-1.5 mm | Standard for general-purpose boilers |
Wall Thickness: >2 mm | Required for high-pressure boilers |
Carefully selecting tube dimensions ensures compatibility with your boiler system’s requirements.
Environmental and Operational Factors
When selecting boiler tubes, it’s important to account for both environmental and operational factors. These considerations affect material longevity and efficiency, particularly in challenging environments.
- Temperature: High-temperature applications need materials like stainless or alloy steel.
- Corrosion Potential: High humidity or chemical exposure requires corrosion-resistant materials.
- Pressure Requirements: Higher pressures demand thicker walls and durable materials.
- Fuel Type: Different fuels generate varying combustion products that can impact material longevity.
Matching the material and type to the operating environment can drastically reduce maintenance costs and downtime.
Cost and Maintenance Implications
Selecting the right boiler tube also involves understanding the long-term costs. Here are some critical factors to keep in mind:
- Initial Material Costs: Stainless steel and alloy steels are more expensive but offer longer service lives.
- Maintenance Frequency: Certain materials, like copper-nickel, require less maintenance but may have higher upfront costs.
- Downtime Impact: Choosing durable tubes can reduce system downtime, which is essential in high-output environments.
Investing in quality materials can often yield lower overall costs due to reduced maintenance and replacement needs over time.
Conclusion
Choosing the right boiler tube for your needs requires a comprehensive understanding of material properties, environmental factors, and cost considerations. By carefully analyzing these factors, you can make a choice that will enhance efficiency, reduce maintenance, and extend the lifespan of your boiler system. Remember, each application is unique, and matching the tube specifications to operational requirements is crucial for optimal performance.
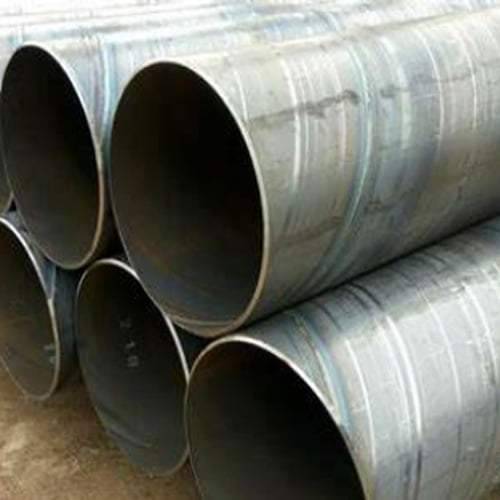
FAQ
Q: What is the best material for high-temperature boiler tubes?
A: Stainless steel and alloy steels are excellent for high-temperature applications due to their heat resistance and durability.
Q: How often should boiler tubes be inspected?
A: Regular inspections should occur annually, with more frequent checks for high-pressure or high-temperature systems.
Q: Can I replace only a few tubes if they’re damaged?
A: While possible, it’s recommended to assess the entire system, as partial replacements may lead to inefficiencies or further issues.
Q: How do I know if my boiler tube needs replacing?
A: Common signs include corrosion, cracks, or a decrease in heating efficiency. Regular inspections help catch these early.
By understanding these key points, you’re better equipped to make an informed decision on the right boiler tube for your specific needs.