Introduction
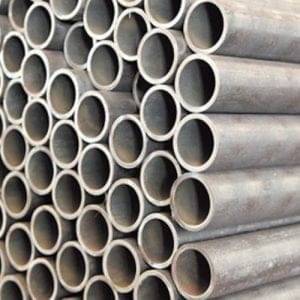
Steel pipe structures have become increasingly popular in modern construction due to their exceptional strength, durability, and versatility. Prefabrication techniques have revolutionized the way these structures are designed and built, offering numerous advantages over traditional methods. This blog delves into the applications and advantages of prefabrication in steel pipe structure design, exploring how these techniques optimize efficiency and enhance project outcomes.
Advantages of Steel Pipe Structures
Steel pipe structures are favored for their robustness and resilience, making them suitable for a wide range of applications. Their high strength-to-weight ratio ensures structural integrity while their durability guarantees longevity. Additionally, steel pipes can be easily shaped and joined, facilitating intricate architectural designs that are both functional and aesthetically pleasing.
Applications in Various Industries
Steel pipe structures find extensive use across diverse industries due to their adaptability and reliability. In infrastructure, they are commonly employed in the construction of bridges, tunnels, and elevated highways, where their load-bearing capacity and resistance to environmental factors are critical. Architecturally, steel pipes are utilized in stadia roofs, architectural facades, and canopies, showcasing their versatility in achieving innovative and eye-catching designs. Furthermore, in industrial settings such as manufacturing facilities, warehouses, and power plants, steel pipe structures provide robust support for heavy machinery and equipment.
Prefabrication Techniques
Prefabrication plays a pivotal role in optimizing the construction of steel pipe structures by shifting fabrication processes away from the construction site. Components are manufactured in controlled environments, ensuring precision and consistency. This off-site approach not only reduces on-site construction time but also minimizes disruptions to surrounding environments. Assembly line production further enhances efficiency, allowing for simultaneous manufacturing of components that can be swiftly assembled on-site.
Case Studies
Examining successful implementations of prefabricated steel pipe structures provides insight into their practical advantages. For instance, in bridge construction, prefabricated steel pipe segments have been utilized to expedite project timelines while maintaining structural integrity. Similarly, in architectural applications, prefabricated steel pipes have enabled the creation of iconic structures that blend functionality with artistic design, underscoring their versatility and aesthetic appeal.
Advantages of Prefabrication
Prefabrication offers several compelling advantages for steel pipe structure design. By reducing on-site construction time, it minimizes labor costs and accelerates project completion. Quality control is significantly enhanced through standardized manufacturing processes, ensuring that each component meets stringent engineering specifications. Moreover, prefabrication promotes sustainability by optimizing material usage and reducing waste, aligning with contemporary environmental standards.
Comparison of Prefabricated vs. Traditional Construction Methods
Aspect | Prefabricated Construction | Traditional Construction |
---|---|---|
Construction Time | Shorter due to simultaneous off-site fabrication | Longer, as all construction is on-site |
Quality Control | High, with controlled manufacturing environments | Variable, depending on on-site conditions |
Material Waste | Reduced, due to precise component manufacturing | Potential for higher waste during assembly |
Cost Efficiency | Often lower due to reduced on-site labor | Can be higher due to extended construction |
Environmental Impact | Lower carbon footprint from minimized on-site work | Higher emissions from on-site activities |
Flexibility in Design | Can accommodate complex designs effectively | Limited by on-site construction capabilities |
Risk of Weather Delays | Minimal, as fabrication is not weather-dependent | High, as weather can delay on-site work |
Environmental Impact
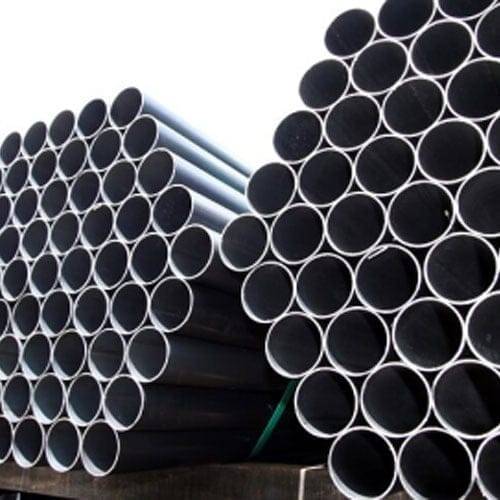
The environmental sustainability of prefabricated steel pipe structures is underscored by their efficient use of materials and recyclability. Steel, being a highly recyclable material, supports sustainable construction practices by minimizing resource depletion and waste generation. Prefabrication further enhances environmental credentials by reducing carbon emissions associated with on-site construction activities, making it a preferred choice for environmentally conscious projects.
Conclusion
In conclusion, prefabrication has emerged as a cornerstone of modern steel pipe structure design, offering unparalleled advantages in terms of efficiency, quality, and sustainability. The adaptability of steel pipes, combined with advanced fabrication techniques, enables the realization of complex architectural visions and robust infrastructure projects. As industries continue to innovate, the integration of prefabricated components ensures that steel pipe structures remain at the forefront of construction advancements, delivering resilient solutions for the built environment.
FAQ
Q: What are the key advantages of using steel pipes in structural design?
A: Steel pipes offer high strength, durability, and versatility in architectural design, making them ideal for various structural applications. Their ability to withstand heavy loads and harsh environmental conditions ensures long-term performance and reliability.
Q: How does prefabrication benefit steel pipe structure construction?
A: Prefabrication reduces on-site construction time, improves quality control, and enhances cost efficiency through streamlined production processes. By manufacturing components in controlled environments, prefabrication ensures precise assembly and reduces material waste.
Q: Are prefabricated steel pipe structures environmentally sustainable?
A: Yes, prefabricated steel pipe structures promote sustainability by minimizing material waste and utilizing recyclable materials. Off-site fabrication reduces carbon emissions associated with transportation and on-site construction activities, supporting eco-friendly building practices.