Welcome to My Blog!
Before we dive into the content, I’d love for you to join me on my social media platforms where I share more insights, engage with the community, and post updates. Here’s how you can connect with me:
Facebook:https://www.facebook.com/profile.php?id=61559060896490
Now, let’s get started on our journey together. I hope you find the content here insightful, engaging, and valuable.
Introduction
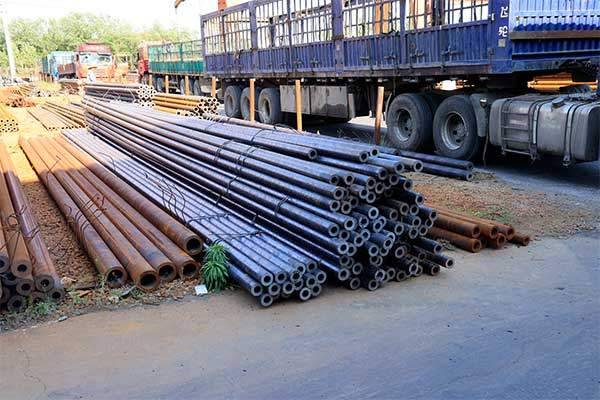
When it comes to selecting mechanical tubing material, the decision can have a significant impact on the performance, durability, and cost-effectiveness of a project. Mechanical tubing is used in a wide range of industries, including automotive, construction, and manufacturing, and each application has unique material requirements. Choosing the right material involves careful consideration of factors such as strength, corrosion resistance, weight, and cost.
In this blog, we’ll delve into the key factors to consider when selecting mechanical tubing material for various industrial applications. We’ll explore different types of materials, their properties, and how these affect the overall performance of your project.
Understanding Mechanical Tubing Materials
Mechanical tubing refers to hollow tubes or pipes that are used in applications where structural integrity and mechanical performance are critical. These tubes are typically made from a variety of materials, including steel, aluminum, and alloys. The material selected for a particular application can dramatically influence the tube’s functionality, durability, and resistance to environmental factors.
Common Types of Mechanical Tubing Materials
There are several types of materials commonly used in mechanical tubing, each with unique characteristics:
- Carbon Steel: Known for its strength and affordability, carbon steel is often used in applications requiring high mechanical properties.
- Stainless Steel: Offers excellent corrosion resistance, making it ideal for environments exposed to moisture and chemicals.
- Aluminum: Lightweight and corrosion-resistant, aluminum is widely used in industries like aerospace and automotive.
- Alloy Steel: Provides enhanced mechanical properties, such as increased strength and toughness, through the addition of elements like chromium, molybdenum, and nickel.
- Titanium: Extremely strong and lightweight, titanium is used in high-performance applications like aerospace and medical devices.
Table: Comparison of Common Mechanical Tubing Materials
Material | Strength | Corrosion Resistance | Weight | Cost | Applications |
---|---|---|---|---|---|
Carbon Steel | High | Low | Heavy | Low | Construction, industrial machinery |
Stainless Steel | Medium-High | Very High | Heavy | Medium-High | Chemical, food processing, medical |
Aluminum | Medium | High | Very Light | Medium | Automotive, aerospace, transportation |
Alloy Steel | Very High | Medium | Heavy | Medium-High | Heavy machinery, power generation |
Titanium | Very High | Very High | Light | Very High | Aerospace, medical implants |
Factors to Consider When Selecting Mechanical Tubing Material
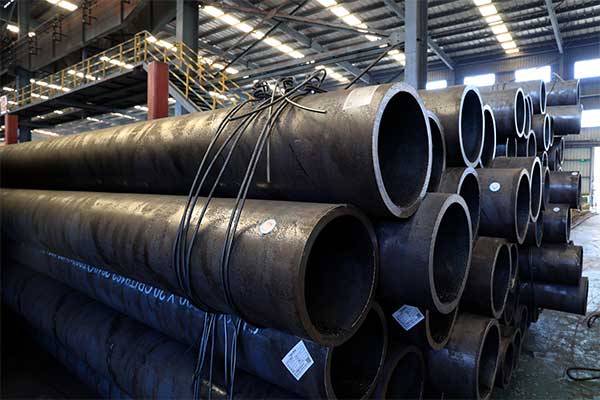
Choosing the right mechanical tubing material for your project requires careful evaluation of several factors. These factors ensure that the material not only meets the functional requirements but also optimizes performance, durability, and cost-effectiveness. Below are the most important considerations:
Strength and Durability
The material’s strength is a crucial factor in mechanical tubing, especially in applications that involve heavy loads, stress, or pressure. Steel and alloy steels are often chosen for their high tensile strength and durability. For high-stress environments, alloy steel and titanium are superior options, as they offer enhanced strength and resistance to fatigue.
Questions to Ask:
- What is the required load-bearing capacity?
- Will the tubing face dynamic or static loads?
- Is impact resistance important for the application?
Corrosion Resistance
Corrosion can significantly shorten the lifespan of mechanical tubing, particularly in harsh environments where the material is exposed to moisture, chemicals, or extreme temperatures. Stainless steel and titanium provide excellent corrosion resistance, making them ideal for use in marine, chemical, and food processing industries. For projects where corrosion is less of an issue, carbon steel or alloy steel may be suitable.
Questions to Ask:
- Will the tubing be exposed to corrosive elements, such as chemicals or saltwater?
- How long should the tubing last before corrosion becomes an issue?
Weight
Weight is another key factor, especially in industries like automotive, aerospace, and transportation, where reducing weight can lead to increased efficiency and performance. Aluminum and titanium are both lightweight options, though they come at a higher cost than steel.
Questions to Ask:
- Is weight reduction a priority for this application?
- How will the weight of the tubing affect the overall system performance?
Cost
Cost is always a significant factor in material selection. While high-performance materials like titanium and stainless steel offer excellent mechanical properties, they come with a higher price tag. Carbon steel, on the other hand, is cost-effective and offers good strength, making it a popular choice for many applications. Striking a balance between performance and cost is essential.
Questions to Ask:
- What is the budget for material costs?
- Can a lower-cost material meet the functional requirements?
Application-Specific Requirements
Certain industries have specialized needs when it comes to mechanical tubing. For example, the medical industry may require materials that are biocompatible, while the aerospace industry demands materials that can withstand extreme temperatures and pressures. Always consider the specific requirements of your application when selecting a material.
Questions to Ask:
- Are there specific industry standards or certifications that the material must meet?
- Will the material need to withstand extreme environmental conditions, such as high heat or pressure?
Conclusion
Selecting the right mechanical tubing material is essential for ensuring the longevity, efficiency, and performance of your project. By considering factors such as strength, corrosion resistance, weight, cost, and application-specific requirements, you can choose a material that best suits your needs. Whether you’re working in construction, manufacturing, or aerospace, making an informed decision about tubing material will ultimately lead to better results and cost savings.
FAQ
What is the most commonly used material for mechanical tubing?
Carbon steel is the most commonly used material for mechanical tubing due to its strength, affordability, and availability. It is widely used in construction, machinery, and industrial applications.
How do I determine which mechanical tubing material is best for my project?
To determine the best material, evaluate factors such as the required strength, corrosion resistance, weight, and cost. Additionally, consider the specific demands of your industry or application to ensure optimal performance.
Is stainless steel worth the higher cost for mechanical tubing?
Stainless steel is often worth the investment if corrosion resistance is a priority in your project. It is especially beneficial in environments exposed to moisture, chemicals, or extreme temperatures.
How does weight impact the selection of mechanical tubing material?
In industries like aerospace and automotive, reducing weight is crucial for improving efficiency and performance. Materials like aluminum and titanium are lightweight options that offer good strength, but they come at a higher cost than steel.
What industries typically use alloy steel for mechanical tubing?
Alloy steel is commonly used in heavy machinery, power generation, and industrial equipment. Its high strength and toughness make it suitable for demanding applications where impact resistance and durability are critical.