1. Raw material preparation:
Prepare the raw materials for hot-rolled seamless steel pipes, including billets and alloy elements.
2. Heating:
Heat the billets to an appropriate temperature, usually above 1150°C.
3. Piercing:
Place the heated billets into a piercing machine to create a rough pipe.
4. Rolling:
Feed the rough pipe into a precision rolling mill, where multiple passes of precision rolling are performed to achieve the desired diameter and wall thickness.
5. Cooling:
After precision rolling, the pipes undergo cooling treatment to gradually reduce their temperature.
6. Sizing:
Process the cooled pipes to achieve precise diameter according to the specified dimensions.
7. Heat treatment:
Subject the sized pipes to heat treatment to improve their mechanical properties and microstructure.
8. Straightening:
Straighten the pipes that have undergone heat treatment to achieve a straight shape.
9. Shot blasting cleaning:
Use shot blasting equipment to clean the surface of the straightened pipes, removing oxide layers and impurities.
10. Inspection:
Perform various inspections on the shot-blasted pipes, including visual inspection, physical property testing, and chemical composition analysis.
11. Marking and packaging:
Mark the qualified pipes and package them for transportation and storage.
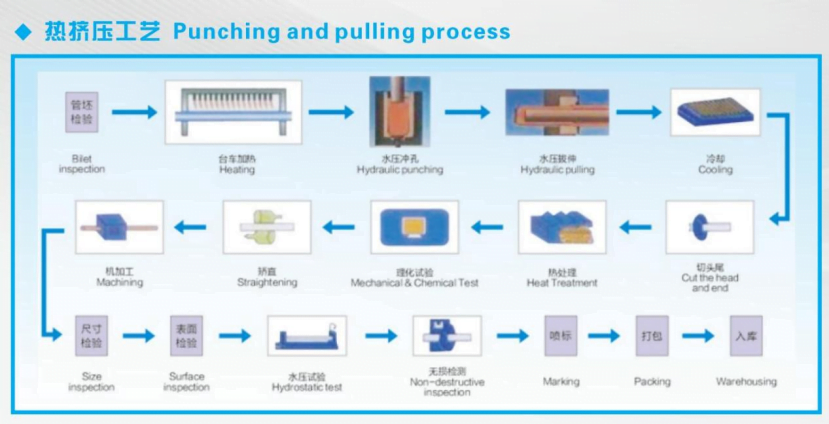
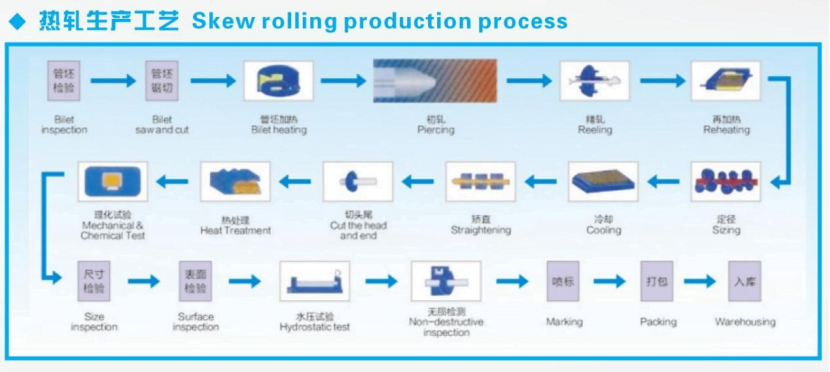
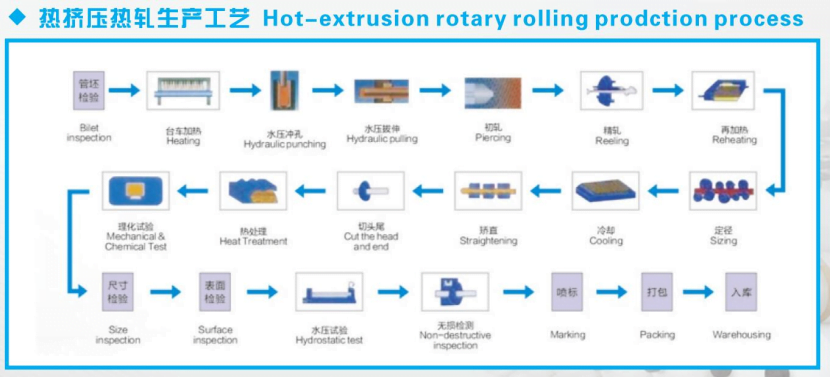