Welcome to My Blog!
Before we dive into the content, I’d love for you to join me on my social media platforms where I share more insights, engage with the community, and post updates. Here’s how you can connect with me:
Facebook:https://www.facebook.com/profile.php?id=61559060896490
Now, let’s get started on our journey together. I hope you find the content here insightful, engaging, and valuable.
Table of Contents
Introduction
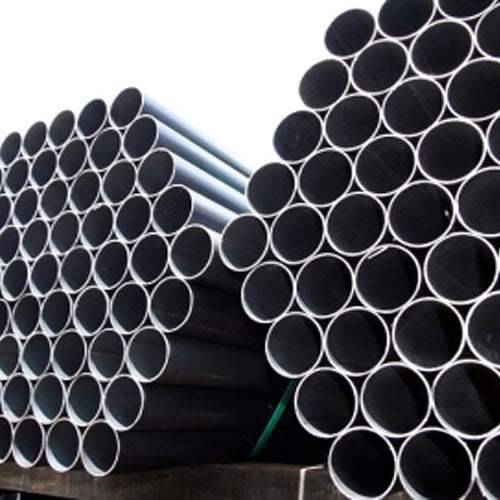
Boiler tubes are critical components in various industries, including power generation, chemical processing, and manufacturing. They are responsible for transferring heat efficiently and safely under high pressure and temperature conditions. Understanding boiler tube specifications is crucial for ensuring the reliability, efficiency, and safety of boiler systems. These specifications define the material properties, dimensions, manufacturing processes, and testing requirements of boiler tubes. Choosing the right boiler tube based on specific application requirements is essential to prevent failures, downtime, and potential hazards. This comprehensive guide delves into the intricacies of boiler tube specifications, providing valuable insights for engineers, technicians, and anyone involved in boiler system design, operation, and maintenance.
Boiler tube specifications are not arbitrary; they are meticulously developed and refined by international standards organizations such as ASTM (American Society for Testing and Materials), ASME (American Society of Mechanical Engineers), EN (European Norms), and JIS (Japanese Industrial Standards). These standards ensure consistency and quality across the industry, facilitating global trade and collaboration. Adhering to these specifications is not only a matter of best practice but often a legal requirement in many jurisdictions.
Key Factors Influencing Boiler Tube Specifications
Several key factors influence the selection and specification of boiler tubes. These factors must be carefully considered during the design and procurement phases to ensure optimal performance and longevity.
Operating Temperature and Pressure:
The operating temperature and pressure of the boiler are primary determinants of the required material strength and thickness of the tubes. Higher temperatures and pressures necessitate stronger alloys and thicker walls to withstand the increased stress. Creep, a gradual deformation under sustained stress at high temperatures, is a critical consideration for high-temperature applications.
Fluid Type and Composition:
The type and composition of the fluid flowing through the tubes (e.g., water, steam, hot gases) also play a significant role. The fluid’s corrosivity, erosivity, and chemical reactivity must be considered when selecting the tube material. For instance, if the fluid contains corrosive elements, corrosion-resistant alloys like stainless steel or nickel alloys might be necessary.
Heat Transfer Requirements:
The required heat transfer rate dictates the tube diameter, wall thickness, and surface finish. Smaller diameter tubes offer a larger surface area for heat transfer but also increase pressure drop. The surface finish can be enhanced with fins or other enhancements to further improve heat transfer efficiency.
Environmental Conditions:
The external environment surrounding the boiler can also impact tube selection. Factors such as ambient temperature, humidity, and exposure to corrosive substances must be taken into account. For example, boilers located in coastal areas might require tubes with enhanced corrosion resistance due to the salty air.
Understanding Material Specifications for Boiler Tubes
Material selection is a cornerstone of boiler tube specifications. The chosen material must possess adequate strength, corrosion resistance, and thermal conductivity for the intended service conditions. Some commonly used materials include:
- Carbon Steel: Economical and suitable for lower temperature and pressure applications.
- Alloy Steel: Offers improved strength, creep resistance, and corrosion resistance at higher temperatures and pressures. Examples include Chrome-Moly steels (e.g., T11, T22, T91).
- Stainless Steel: Provides excellent corrosion resistance and is often used in applications involving corrosive fluids or environments.
- Nickel Alloys: Offers exceptional high-temperature strength and corrosion resistance, suitable for extreme service conditions.
Each material is assigned specific designations according to standards like ASTM and ASME, which define its chemical composition, mechanical properties, and heat treatment requirements. These designations are crucial for ensuring material traceability and quality control.
Dimensional Specifications of Boiler Tubes
Boiler tube specifications also define the dimensional characteristics of the tubes, including:
- Outer Diameter (OD): The external diameter of the tube.
- Wall Thickness (WT): The thickness of the tube wall.
- Length: The overall length of the tube.
These dimensions are typically specified in inches or millimeters. Tolerances on these dimensions are also defined to account for manufacturing variations. The relationship between OD and WT is crucial for determining the tube’s pressure-bearing capacity.
Manufacturing and Testing Requirements for Boiler Tubes
Boiler tubes are manufactured using various processes, including:
- Seamless Manufacturing: The tube is formed from a solid billet of steel, resulting in a tube without any welds. This is preferred for high-pressure applications.
- Welded Manufacturing: The tube is formed by welding together steel plates or strips. This is more economical for lower pressure applications.
Regardless of the manufacturing process, rigorous testing is essential to ensure the quality and integrity of the tubes. Common tests include:
- Hydrostatic Testing: The tube is pressurized with water to verify its pressure-bearing capacity.
- Non-Destructive Testing (NDT): Techniques like ultrasonic testing, eddy current testing, and radiographic testing are used to detect internal and surface defects without damaging the tube.
Boiler Tube Specifications Table
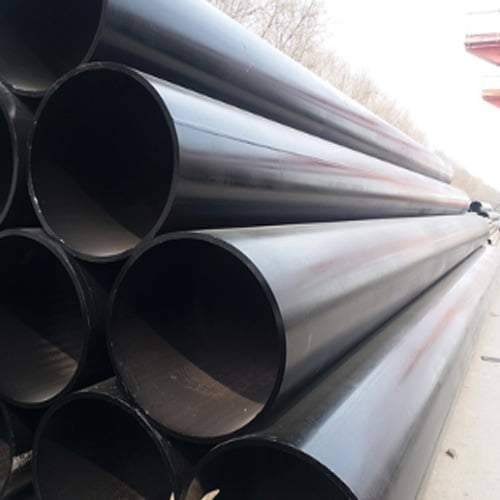
The following table presents a simplified overview of common boiler tube specifications and their typical applications. It’s important to consult relevant standards for detailed information.
Specification | Material | Typical Application | Operating Temperature (°C) | Operating Pressure (MPa) |
---|---|---|---|---|
ASTM A178 | Carbon Steel | Fire-tube boilers, low-pressure applications | Up to 450 | Up to 2 |
ASTM A192 | Carbon Steel | Water-tube boilers, high-pressure applications | Up to 500 | Up to 10 |
ASTM A213 T11 | Alloy Steel (1.25% Cr, 0.5% Mo) | Superheaters, reheaters | Up to 550 | Up to 20 |
ASTM A213 T22 | Alloy Steel (2.25% Cr, 1% Mo) | High-temperature superheaters | Up to 600 | Up to 30 |
ASTM A213 T91 | Alloy Steel (9% Cr, 1% Mo, V, Nb) | Advanced power plants, ultra-supercritical boilers | Up to 650 | Up to 40 |
EN 10216-2 16Mo3 | Alloy Steel (0.3% Mo) | Boiler and heat exchanger tubes | Up to 500 | Up to 25 |
JIS G3454 STPG370 | Carbon Steel | General service boiler tubes | Up to 350 | Up to 1.5 |
Conclusion
Adhering to correct boiler tube specifications is paramount for ensuring the safe and efficient operation of boiler systems. Selecting the appropriate materials, dimensions, and manufacturing processes based on the specific service conditions is crucial for preventing failures, minimizing downtime, and ensuring the longevity of the equipment. Understanding boiler tube specifications helps engineers, technicians, and operators make informed decisions regarding design, procurement, installation, maintenance, and repair. Consulting relevant international standards and working with reputable suppliers is essential for obtaining high-quality boiler tubes that meet the required specifications. By prioritizing adherence to boiler tube specifications, industries can enhance safety, improve efficiency, and reduce operational costs.
FAQ
What is the difference between ASTM and ASME boiler tube specifications?
ASTM develops material specifications (e.g., chemical composition, mechanical properties), while ASME develops construction codes (e.g., design, fabrication, inspection) that reference ASTM materials. In the context of boiler tubes, ASTM defines the materials used to make the tubes, and ASME provides the rules for how those tubes are used in boiler construction.
How do I determine the appropriate boiler tube material for my application?
The appropriate material depends on several factors, including operating temperature and pressure, fluid type and composition, heat transfer requirements, and environmental conditions. Consulting relevant standards and seeking expert advice from material specialists is recommended.
What is the significance of non-destructive testing (NDT) for boiler tubes?
NDT methods are crucial for detecting internal and surface defects in boiler tubes without causing damage. These tests help ensure the integrity and reliability of the tubes, preventing potential failures during operation.