Welcome to My Blog!
Before we dive into the content, I’d love for you to join me on my social media platforms where I share more insights, engage with the community, and post updates. Here’s how you can connect with me:
Facebook:https://www.facebook.com/profile.php?id=61559060896490
Now, let’s get started on our journey together. I hope you find the content here insightful, engaging, and valuable.
Steel production is an essential part of the industrial world, laying the foundation for countless structures, machines, and technologies that define modern society. The steel process, from raw materials to finished products, involves multiple stages designed to ensure quality, efficiency, and precision. This blog will break down each stage of the steel process, providing you with an in-depth understanding of how steel is made and refined to meet the highest standards.
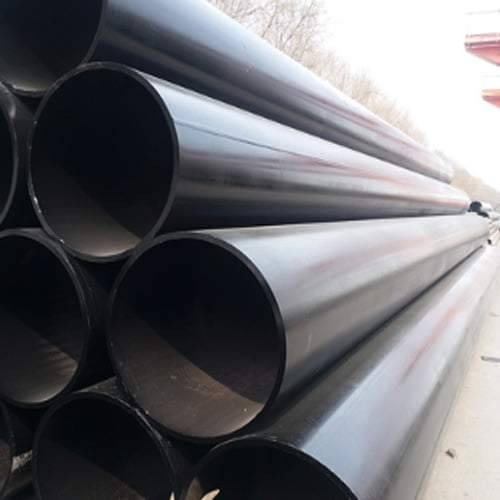
Introduction
In this comprehensive guide, we will explore each essential stage of the steel process, including the science behind converting raw materials into high-quality steel products. With a focus on each stage’s purpose, tools, and techniques, we aim to provide a clear understanding of what makes the steel process so vital to modern manufacturing.
Raw Materials Selection
The steel process begins with selecting the right raw materials. These typically include iron ore, coal, and limestone. Each of these materials serves a unique purpose in the steel process:
Material | Purpose |
---|---|
Iron Ore | Primary source of iron |
Coal (Coke) | Acts as fuel and reducing agent |
Limestone | Removes impurities, forming slag |
Selecting the correct grade and quality of each material directly influences the overall quality of the final steel product.
Ironmaking Process
The ironmaking stage is crucial, as this is where iron ore is transformed into molten iron. Typically, this is achieved in a blast furnace. Here’s how it works:
- Blast Furnace: The iron ore, coke, and limestone are added to a blast furnace, where intense heat (over 2,000°C) causes a chemical reaction. This reaction removes oxygen from the iron ore, producing molten iron.
- Formation of Slag: Impurities from the iron are combined with limestone to form slag, which is removed from the furnace.
This process is vital as it prepares the iron for further refinement in the steelmaking process.
Steelmaking: Converting Iron to Steel
Once iron is extracted, the next step in the steel process is converting this molten iron into steel. This is primarily done through one of two methods:
- Basic Oxygen Furnace (BOF): Oxygen is blown into the molten iron to reduce carbon content and other impurities.
- Electric Arc Furnace (EAF): Uses electricity to melt scrap steel and convert it into new steel products.
This stage gives manufacturers control over the steel’s carbon content, enhancing strength and durability.
Secondary Refining for Purity
Secondary refining focuses on removing remaining impurities to ensure high-quality steel. This stage involves:
- Ladle Refining: Adding elements like argon or calcium to remove sulfur, phosphorus, and other impurities.
- Vacuum Degassing: Steel is placed under vacuum conditions to remove dissolved gases like hydrogen and nitrogen.
Casting: Shaping Steel
Casting involves pouring molten steel into molds to create the desired shape. There are two primary casting methods:
- Continuous Casting: Steel is poured continuously into a mold, creating long slabs, billets, or blooms.
- Ingot Casting: Steel is poured into individual molds to form large blocks, which are later cut and processed.
Each casting type is chosen based on the end product’s size, shape, and desired properties.
Casting Method | Characteristics |
---|---|
Continuous Casting | Produces long slabs, high efficiency |
Ingot Casting | Creates large blocks, used for specialty steels |
Hot and Cold Rolling Processes
Rolling involves reducing the thickness of steel slabs or blooms and creating a uniform shape. There are two types of rolling processes:
- Hot Rolling: Steel is heated above its recrystallization temperature, then passed through rollers. Hot rolling is ideal for creating flat products, sheets, and structural components.
- Cold Rolling: Steel is rolled at room temperature to improve surface finish, tolerance, and strength. It is often used for creating steel with a smoother finish and higher precision.
Heat Treatment and Finishing
Heat treatment refines steel’s mechanical properties, including hardness, toughness, and ductility. Common heat treatment processes include:
- Annealing: Softens steel, improving workability.
- Quenching: Rapid cooling to increase hardness.
- Tempering: Reduces brittleness while maintaining hardness.
In finishing, steel may undergo surface treatments like galvanizing, painting, or polishing to enhance durability, corrosion resistance, or aesthetic appeal.
Quality Control in the Steel Process
Quality control is integrated into every stage of the steel process to ensure high standards. Common quality control measures include:
- Spectrometry: Analyzing the chemical composition to ensure it meets specifications.
- Ultrasonic Testing: Detecting internal defects and cracks.
- Hardness Testing: Assessing material strength and toughness.
Applications of Various Steel Types
Each type of steel has unique applications:
Steel Type | Applications |
---|---|
Carbon Steel | Automotive parts, construction |
Alloy Steel | Tools, machinery, aerospace components |
Stainless Steel | Kitchenware, medical devices, architectural finishes |
Tool Steel | Cutting tools, molds, and dies |
Understanding these applications provides insight into why the steel process is tailored for different end products.
Conclusion
The steel process is complex, involving numerous steps to transform raw materials into high-quality steel products used in various industries. From raw material selection to quality control, each stage is essential for producing steel that meets specific industrial standards. By understanding these essential stages, you gain insight into the meticulous process behind one of the world’s most essential materials.
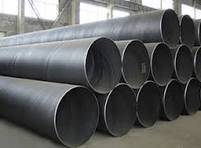
FAQ
Q1: Why is the steel process essential?
A1: The steel process ensures the production of high-quality steel with controlled properties, meeting the needs of industries like construction, automotive, and manufacturing.
Q2: What is the most common steelmaking method?
A2: The Basic Oxygen Furnace (BOF) is one of the most widely used methods, known for its efficiency and ability to produce high-quality steel.
Q3: How is steel quality controlled?
A3: Quality control involves testing for chemical composition, structural integrity, and mechanical properties to ensure consistency and durability.
This guide on Understanding the Essential Stages of the Steel Process provides a comprehensive look at how raw materials become the versatile steel products essential to our world.