Welcome to My Blog!
Before we dive into the content, I’d love for you to join me on my social media platforms where I share more insights, engage with the community, and post updates. Here’s how you can connect with me:
Facebook:https://www.facebook.com/profile.php?id=61559060896490
Now, let’s get started on our journey together. I hope you find the content here insightful, engaging, and valuable.
Table of Contents
Introduction
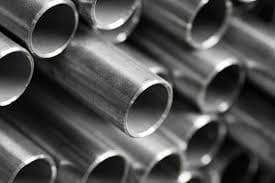
In today’s fast-changing industrial world, boiler tube coating technology plays a more crucial role than ever before. Whether you’re in power generation, petrochemical production, or heavy machinery, the need for reliable and durable seamless steel tubes and superior coating solutions has never been greater. Why? Because efficient coatings protect tubes against corrosion, oxidation, and extreme temperatures—ensuring safety, longevity, and energy savings.
But here’s something you might not have realized: not all coatings are created equal. The latest innovations go far beyond traditional methods to meet the rising demands of various industries. In this article, we’ll guide you through what’s trending in boiler tube coating technology, how these advancements can impact your operations, and what you need to consider when choosing the right coating solution for your seamless steel tubes.
The Importance of Boiler Tube Coating in Seamless Steel Tube Applications
Let’s start with a simple question: Why coat boiler tubes at all?
Seamless steel tubes—renowned for their strength and reliability—are at the core of countless industrial boilers. But without proper coating, these tubes are vulnerable to:
- High-temperature oxidation
- Stress corrosion cracking
- Erosion from particles in steam or flue gas
- Fatigue damage due to thermal cycling
By applying cutting-edge boiler tube coating technologies, industries can:
- Extend tube service life by reducing corrosion.
- Maintain optimal thermal conductivity.
- Minimize maintenance costs and unplanned downtimes.
- Improve energy efficiency in boilers.
Coatings are no longer a luxury—they’re an absolute necessity in the demanding environments where seamless steel tubes are used.
Latest Innovations in Boiler Tube Coating Technology
1. Thermal Spray Coatings: The New Standard in Protection
One of the most significant advances is thermal spray technology, especially High-Velocity Oxygen Fuel (HVOF) coatings. These coatings form a dense, hard barrier that resists wear, corrosion, and oxidation at high temperatures—ideal for seamless steel tube applications in boilers.
Key Benefits:
- Excellent bond strength
- Reduced porosity
- Enhanced resistance to slag and ash deposits
2. Nano-Coatings: The Invisible Armor
Yes, nanotechnology has entered the world of boiler tube coating. Ultra-thin layers applied on tube surfaces offer a powerful shield against chemical attack and thermal degradation. Despite their microscopic thickness, these coatings significantly enhance the lifespan of seamless tubes without affecting heat transfer efficiency.
Why choose nano-coatings?
- Minimal impact on tube dimensions
- Improved resistance to acidic environments
- Low friction, reducing wear
3. Ceramic-Based Coatings: High-Temperature Champions
If your boiler system runs at extreme temperatures, ceramic-based coatings are becoming the go-to solution. Their stability at temperatures exceeding 1000°C makes them perfect for seamless steel tubes in high-stress applications.
Advantages:
- Exceptional thermal barrier performance
- Resistance to thermal shock
- Long-lasting corrosion protection
Comparative Table: Boiler Tube Coating Technologies at a Glance
Here’s a simple table to help you compare the most common boiler tube coating technologies available today:
Coating Technology | Thermal Resistance | Corrosion Protection | Wear Resistance | Application Suitability | Lifespan Enhancement |
---|---|---|---|---|---|
HVOF Thermal Spray | Excellent (up to 900°C) | Very High | High | Power Generation, Refineries | 3x–5x |
Nano-Coatings | Moderate (up to 600°C) | High | Moderate | Chemical Processing, Marine | 2x–3x |
Ceramic-Based Coatings | Outstanding (up to 1200°C) | Excellent | High | High-Temperature Boilers | 4x–6x |
Metallic Overlay Coatings | Good (up to 700°C) | Moderate | Moderate | General Industry Applications | 1.5x–2x |
Diffusion Coatings | Excellent (up to 950°C) | High | High | Aerospace, Power Plants | 3x–4x |
How to Choose the Right Boiler Tube Coating for Your Needs
Selecting the ideal boiler tube coating isn’t just a technical decision—it’s a strategic one. Here are key factors to consider:
- Operating Temperature Range
Higher temperatures demand ceramic or HVOF coatings for lasting performance. - Corrosive Environment Level
In highly acidic or saline atmospheres, nano-coatings can offer unparalleled protection without bulk. - Wear and Erosion Potential
If particulate matter is an issue (as in some fluidized bed combustors), thermal sprays or diffusion coatings provide superior defense. - Budget and Maintenance Considerations
Some coatings may offer short-term savings but require more frequent maintenance; others are more costly upfront but pay off long-term. - Compatibility with Seamless Steel Tubes
Not every coating bonds well with seamless steel tube surfaces; always confirm compatibility to prevent adhesion failures.
Future Trends in Boiler Tube Coating Technology
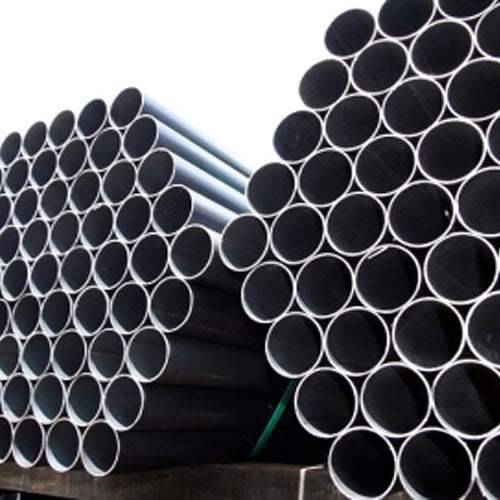
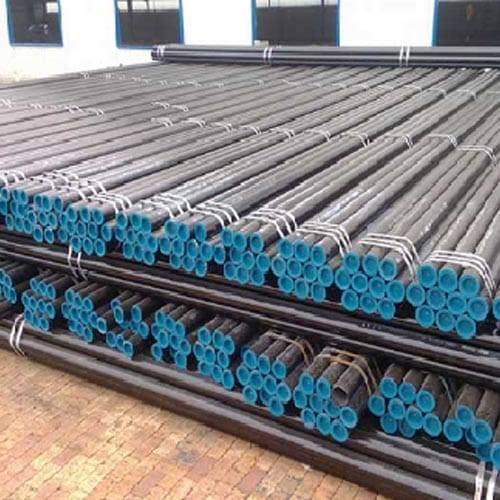
As industries push for higher energy efficiency and stricter environmental regulations, boiler tube coating technology continues to evolve:
- Smart Coatings: Materials that can self-heal or indicate wear through color change are in development.
- Eco-Friendly Coatings: Low-VOC (Volatile Organic Compounds) and non-toxic coating options are gaining traction.
- Advanced Multi-Layer Systems: Combining ceramic and metallic layers to balance thermal resistance with mechanical flexibility.
Expect seamless steel tube manufacturers and boiler operators alike to increasingly demand these high-performance, next-generation coatings to stay competitive.
Conclusion
No matter your industry, your seamless steel tubes face some of the harshest environments known to man. Without the right boiler tube coating, your systems are at risk of premature failure, costly repairs, and reduced efficiency.
The good news? With the latest innovations—thermal sprays, nano-coatings, ceramics—you can dramatically extend your boiler’s life, cut operating costs, and improve safety.
Choosing wisely today means fewer headaches tomorrow. Stay informed, consult coating specialists, and consider your specific operational needs to get the best from your seamless steel tubes and boiler systems.
FAQ
What is the main purpose of boiler tube coating?
The primary purpose is to protect seamless steel tubes from corrosion, oxidation, wear, and thermal stress, which helps extend their service life and maintain system efficiency.
How do I know which boiler tube coating is suitable for my boiler system?
Consider factors such as operating temperature, environment (corrosive or not), mechanical wear, and tube material. Consult with coating specialists for tailored recommendations.
Is there any maintenance required for coated boiler tubes?
Yes. Regular inspections are crucial to monitor coating integrity. While high-quality coatings reduce maintenance frequency, no coating lasts forever without proper care.
Are boiler tube coatings environmentally friendly?
Newer technologies prioritize low-VOC emissions and non-toxic materials, making many modern coatings more eco-friendly than older systems.