Introduction
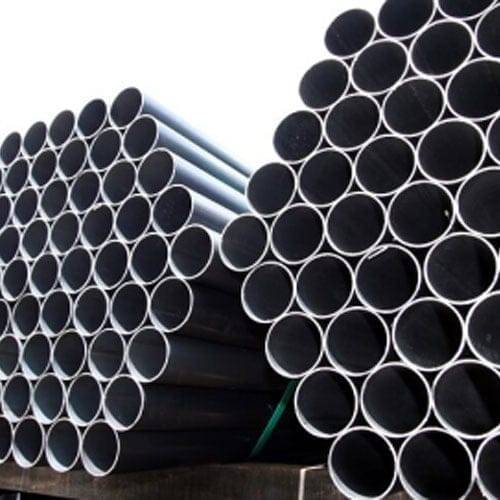
Hydraulic tubing is a fundamental component in industrial machinery, enabling the efficient transmission of fluids under high pressures. This blog delves into the critical role of hydraulic tubing, exploring its types, materials, applications, and the factors to consider when selecting the right tubing for specific industrial needs.
Importance of Hydraulic Tubing
In industrial settings, hydraulic systems are ubiquitous, powering machinery and equipment across sectors such as manufacturing, construction, mining, and aerospace. Hydraulic tubing serves as the arteries of these systems, carrying hydraulic fluids under immense pressure to facilitate movement, lifting, steering, and braking operations. Its reliability directly impacts the efficiency, safety, and productivity of industrial processes.
Types of Hydraulic Tubing
Hydraulic tubing comes in various types, each designed to meet specific operational requirements. Seamless tubing, manufactured without welded seams, offers superior strength and reliability, making it suitable for high-pressure applications where leakage must be minimized. Welded tubing, on the other hand, is more cost-effective and versatile for less demanding environments. Additionally, coiled tubing provides flexibility and compactness, ideal for applications where space is limited or where movement and flexibility are necessary.
Materials Used in Hydraulic Tubing
The choice of material for hydraulic tubing depends on factors such as the type of fluid being conveyed, environmental conditions, and mechanical stress. Common materials include stainless steel, carbon steel, and various alloys. Stainless steel tubing is prized for its high corrosion resistance, making it ideal for applications where fluids with corrosive properties are used. Carbon steel tubing is cost-effective and offers good strength, while alloy steel tubing provides enhanced mechanical properties such as higher tensile strength and hardness, suitable for heavy-duty applications.
Applications of Hydraulic Tubing
Hydraulic tubing finds widespread application in industrial machinery and equipment. For instance, in manufacturing, hydraulic tubing is integral to hydraulic presses, injection molding machines, and assembly lines where precision control and high force are required. In construction, hydraulic systems power cranes, excavators, and bulldozers, enabling heavy lifting and earthmoving operations. Aerospace applications rely on hydraulic tubing for landing gear systems and flight control mechanisms, where reliability and lightweight construction are crucial.
Advantages of Using Hydraulic Tubing
The advantages of hydraulic tubing are manifold. By providing a sealed pathway for hydraulic fluids, tubing minimizes the risk of leaks, ensuring operational safety and environmental compliance. Its ability to withstand high pressures and temperature extremes enhances system durability, reducing downtime and maintenance costs. Moreover, hydraulic tubing facilitates precise control over fluid flow and pressure, contributing to the efficiency and performance of industrial processes.
Case Studies and Examples
Case studies illustrate the practical benefits of hydraulic tubing in real-world applications. For instance, in the automotive industry, hydraulic tubing in power steering systems ensures responsive vehicle handling and driver comfort. Similarly, in mining operations, hydraulic tubing supports the heavy-duty requirements of drilling rigs and hydraulic shovels, operating reliably in harsh conditions to maintain continuous production.
Key Considerations in Choosing Hydraulic Tubing
Selecting the right hydraulic tubing involves evaluating several key factors. These include pressure rating, temperature range, chemical compatibility with hydraulic fluids, resistance to corrosion and abrasion, and compliance with industry standards such as ASTM and SAE specifications. Additionally, considerations such as ease of installation, maintenance requirements, and overall lifecycle costs play a crucial role in determining the optimal tubing solution for specific applications.
Comparison of Hydraulic Tubing Materials
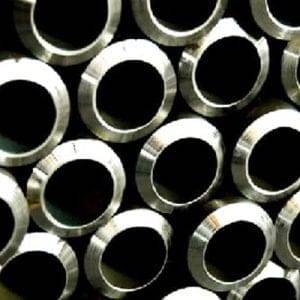
Material | Advantages | Disadvantages |
---|---|---|
Stainless Steel | High corrosion resistance, durability | Higher cost compared to carbon steel |
Carbon Steel | Cost-effective, good strength | Prone to corrosion without proper treatment |
Alloy Steel | Enhanced mechanical properties (strength, hardness) | More complex fabrication, higher cost |
Conclusion
Hydraulic tubing is indispensable in modern industrial applications, providing reliable fluid transmission for enhanced operational efficiency and safety. Understanding the types, materials, applications, and selection criteria for hydraulic tubing is crucial for optimizing performance and minimizing downtime in industrial operations.
FAQ
Q:What are the primary applications of hydraulic tubing?
A:Hydraulic tubing is essential in industries such as manufacturing, construction, mining, and aerospace, where precise fluid control and high force transmission are critical.
Q:How do you choose the right hydraulic tubing material?
A:Factors such as fluid compatibility, environmental conditions, mechanical stress, and budget considerations influence the selection of hydraulic tubing material.
Q:Why is corrosion resistance important in hydraulic tubing?
A:Corrosion resistance ensures the longevity and reliability of hydraulic tubing, reducing maintenance costs and preventing fluid contamination.
Q:What are the advantages of seamless hydraulic tubing?
A:Seamless tubing offers superior strength and reliability due to its uniform structure and absence of welded seams, minimizing the risk of leakage.
Q:How does hydraulic tubing contribute to energy efficiency?
A:By enabling precise control over fluid flow and pressure, hydraulic tubing reduces energy consumption in industrial applications, improving overall efficiency.